Pdca Act Action
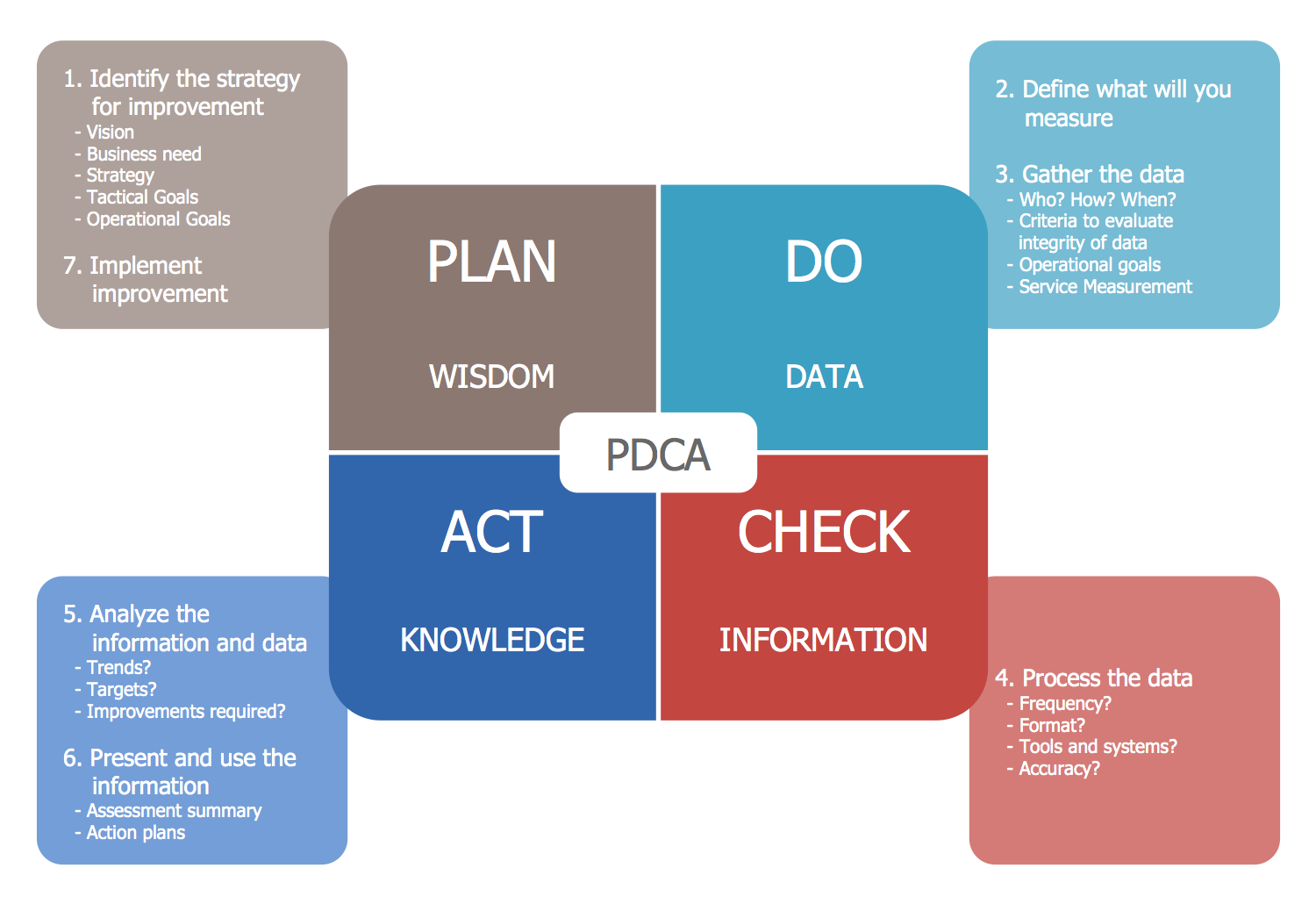
Plan Do Check Act Pdca Solution Conceptdraw Com
What Is The Plan Do Check Act Cycle
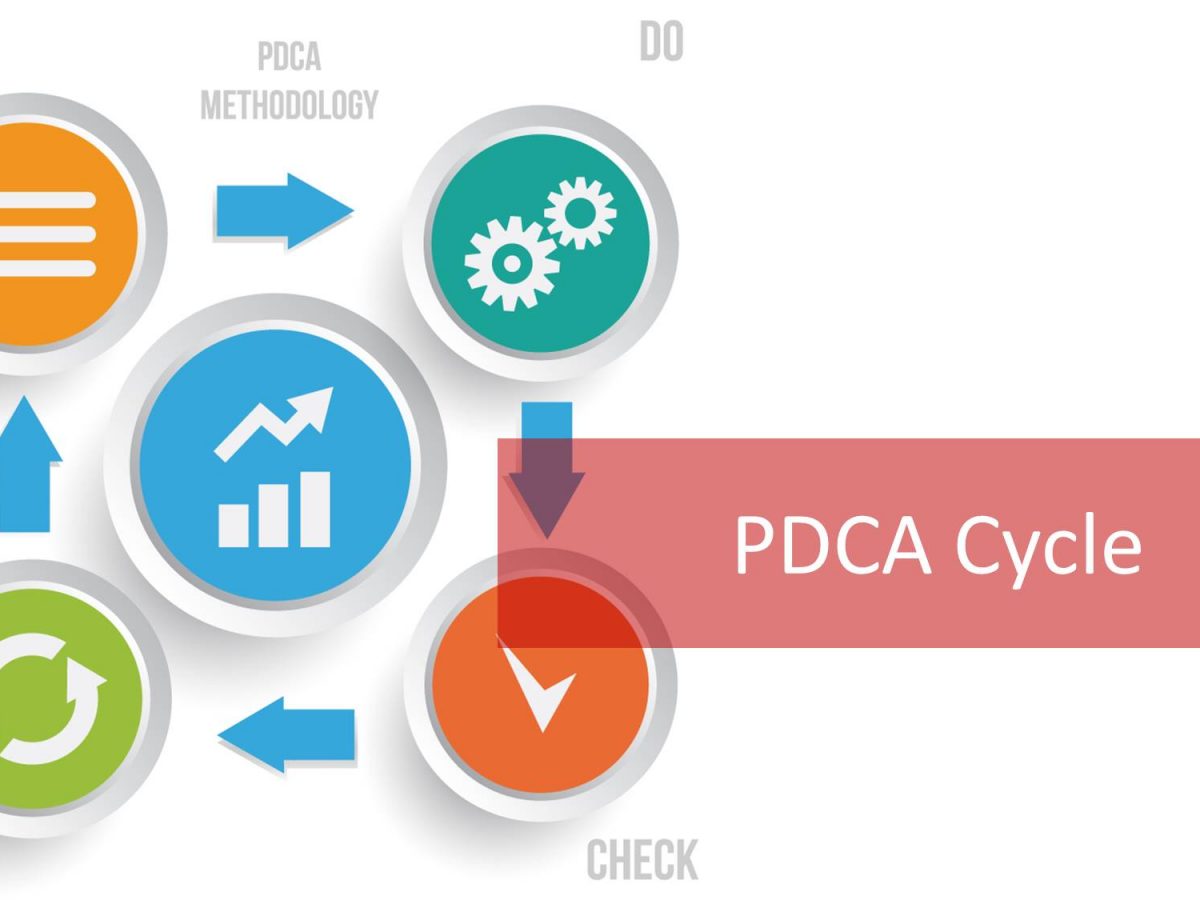
Pdca Cycle The 4 Gears Of Continual Service Improvement
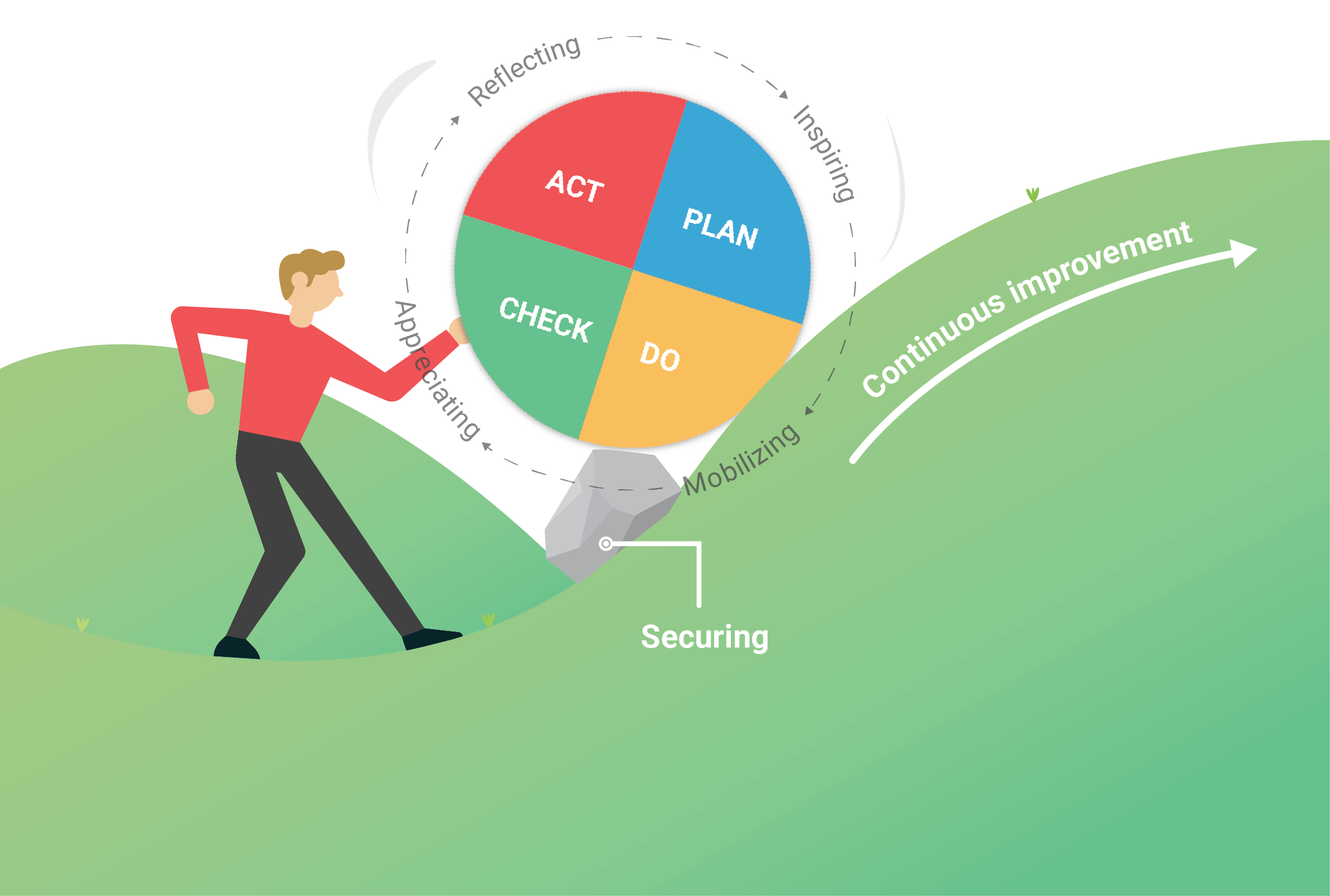
Make Kpis Measurable Operationalize Kpis Kpi Pdca

Auditing For Control And Improvement Qualitywbt
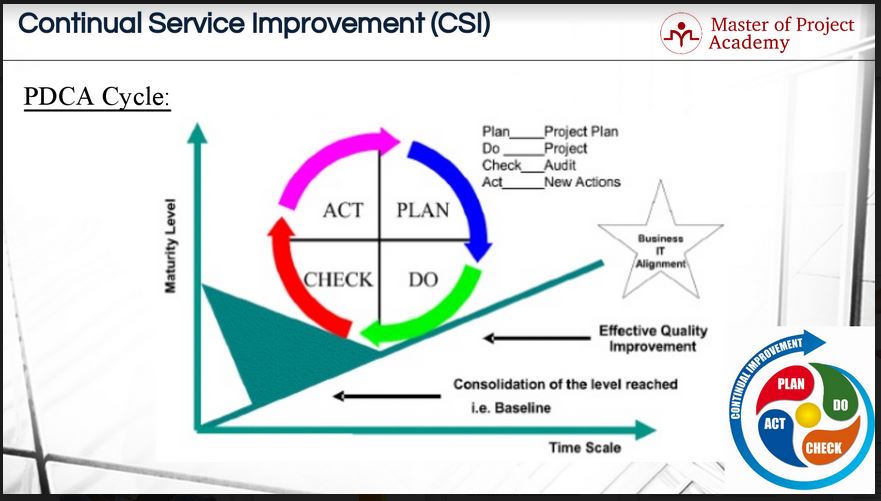
Pdca Cycle The 4 Gears Of Continual Service Improvement
Deming’s PDCA cycle is still the foundation of achieving success using management information, KPIs, and data analytics.
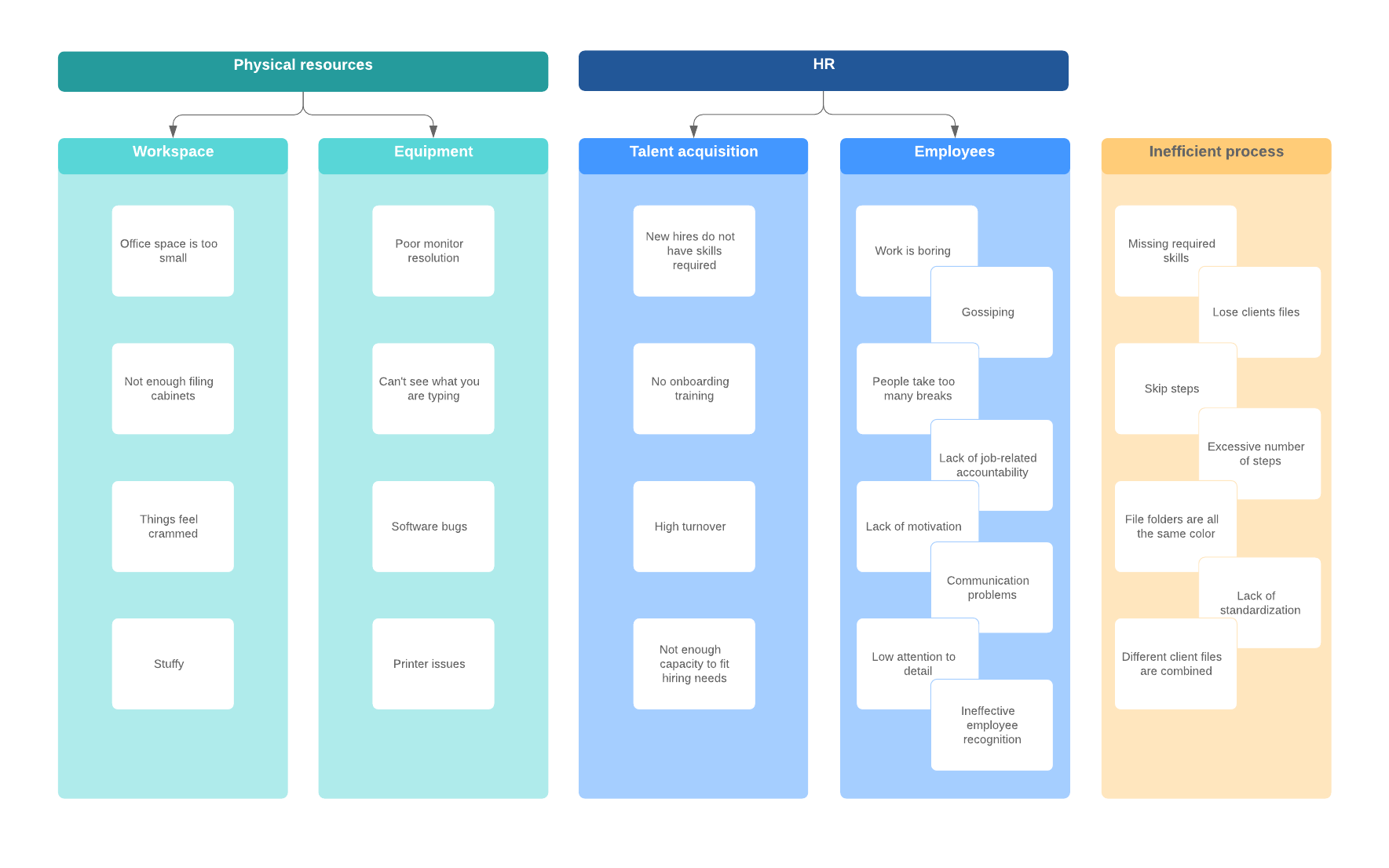
Pdca act action. Welcome to the Plan-Do-Check-Act (PDCA) Tutorial Learning Objectives List the main problem solving steps of Plan-Do-Check-Act (PDCA) Identify quality improvement tools and resources for use in public health Home | Introduction to PD. PDCA –A3 lean.ohio.gov PDCA Method Plan Recognize an opportunity;. And PDCA's "Plan" phase includes much more than what one normally associates with the planning process.
–If the change did not work, go through the cycle again. It was used to improve the production process in the U.S. Pdca – act This phase is all about the actions taken to close the issues/gaps that are identified during the ‘Check’ phase.
When to use the PDCA cycle;. The 4 Activities of the PDCA Cycle Plan. When to Use the PDCA Cycle.
This cycle may be used to improve, for example, an online ordering service or the Service Level Management process within an organization. During World War II. Carry out a small-scale pilot Check Review the test, analyze the results and identify what you’ve learned Act Take action based on what you learned:.
The PDCA concept usually refers to the famous administrator who popularized it:. Plan a change Do Test the change. Konsep siklus PDCA (Plan, Do, Check dan Act) ini pertama kali diperkenalkan oleh seorang ahli manajemen kualitas dari Amerika Serikat yang bernama Dr.
How to run a PDCA cycle yourself. I know many of us have been exposed to Plan-Do-Check-Action (PDCA), (note some earlier versions from Deming the PDSA (Plan- Do-Study-Act) cycle). Used PDCA cycle for one of their corrective action for oversize hub production from a line of automatic manufacturing machines.
PDCA (Plan-Do-Check-Act) is an iterative, four-stage approach for continually improving processes, products or services, and for resolving problems. Using this form can be helpful to primary care practices following the Model for Improvement quality improvement approach. The plan-do-check-act (PDCA) cycle is an iterative and repetitive four-stage approach used in business process management for continuously improving processes, products, and services.
It’s also the last letter in PDCA. Lean Manufacturing PDCA Deming Plan, Do, Check, Act (PDCA) The Deming Cycle Lean Manufacturing Tools and Techniques. I i 4 Key Figures in PDCA.
Pillars explored through the Quality Storyboard methodology aim to identify problems, moving onto the designing and execution of an action plan, verification of results, and validation of a new standard to be adopted and. This is essentially a PDCA loop in action. It is best to use the PDCA cycle when, as defined by ASQ:.
The PDCA methodology is a tool designed to help in improving management, much like methodologies such as OKR and FCA. Deming’s focus was on industrial production processes, and the level of improvements he sought were on the level of production. I know many of us have been exposed to Plan-Do-Check-Action (PDCA), (note some earlier versions from Deming the PDSA (Plan- Do-Study-Act) cycle).Both being a scientific, process oriented, approach.
The way it does this is through identifying errors, creating hypotheses to deal with them, testing the method, and acting on the results. ¾ The PDCA cycle can be an effective and rapid method for implementing continuous improvement. It is an essential component of lean manufacturing.
Going through the prescribed four steps guides the thinking process into breaking down the task into steps and then evaluating the outcome, improving on it, and testing again. PDCA (Plan-Do-Check-Act) is a four-step cycle for continuous improvement. It works on the improvement of activities (such as projects and processes essential to the functioning of an organization) and in solving problems, large or small, that reach these activities.
PDCA (Plan-Do-Check-Act) finds widespread application as a quality management tool. They can provide feedback about what works and what doesn't. It is an iterative cycle which guarantees improvements for the disconnects using examples Shewart cycle (PDCA) to what is now referred to as the Deming Cycle (Plan, Do, Study, Act).
PDCA (plan–do–check–act or plan–do–check–adjust) is an iterative four-step management method used in business for the control and continuous improvement of processes and products. Plan, Do, Check, and Act are critical for consistent implementation of successful process improvements. Plan, Do, Check, Act.
PDCA is based on the “Shewhart cycle,” and was made popular by Dr. Plan Do Study Act (PDSA) Form (PDF, 971 KB, 2 pages) Practices can use this fillable Plan Do Study Act (PDSA) tool to design and test changes to improve health care quality. PDCA stands for Plan-Do-Check-Act – a four-stage problem-solving model that enables organizations to continually improve processes, products or services.
This also makes A the first step in the Continue Reading. PDCA is the basic structure for the district’s overall strategic planning, needs–analysis, process design and delivery, staff goal-setting and evaluation. It is one of the approaches of Total Quality Management and the base for Six Sigma's DMAIC initiative.
One of the major disadvantages of the PDCA methodology is its oversimplification of the improvement process. Deming was responsible for its widespread circulation which eventually got the concept to Japan where it was applied in businesses there. It’s the first letter in the alphabet.
Decide on changes needed to improve the process Deming’s PDCA cycle can be illustrated as follows:. PDCA for Quality Management entails a continuous cycle of analysis, measurement and corrective action to improve the product or process as per customer requirements. It is also known as the Deming Cycle, Shewhart cycle and Deming Wheel.
This model is also referred to as the Deming cycle, Shewhart cycle, plan-do-check-adjust, or plan–do–study–act (PDSA). PDCA is a common model and it is known by many people. The PDCA cycle is a four-step problem solving iterative technique used to improves business processes and bring about change.
PDCA is a continuous improvement tool that is widely used in the services and. Plan, Do, Check, Act(ualize). Plan, Do, Check and Act.
The PDCA model was developed in the 1950s by William Deming as a learning or improvement process based on the scientific method of problem-solving. The PDCA cycle is used in management and manufacturing. In that presentation, Deming described the continuous improvement cycle proposed by Shewhart in the 1939 book, “Statistical Method from the Viewpoint of Quality Control,” which was based on the scientific method that had emerged much earlier in the 1600’s.
Plan Do Check Act (PDCA) template for PowerPoint is a fully editable template based on the PDCA cycle developed by W. Task is to keep trying to improve the process with different plan. The PDCA cycle is considered a project planning tool.
Pengertian dan Siklus PDCA – PDCA adalah singkatan dari PLAN, DO, CHECK dan ACT yaitu siklus peningkatan proses (Process Improvement) yang berkesinambungan atau secara terus menerus seperti lingkaran yang tidak ada akhirnya. Walter Shewhart first introduced the PDCA cycle and was later developed upon by Dr. Other terms of the PDCA cycle include the Deming circle, the Shewhart cycle, the control circle, or the Plan-Do-Study-Act (PDSA) cycle.
While it was made famous by Toyota, the concept was created by legendary management consultant Dr. PDCA Cycle is a continuous process until we achieve our goals which we planned. PDCA cycle stands for the Plan-Do-Check-Act cycle and is a tool commonly used for project planning and continuous improvement.
Edwards Deming, considered by many to be the father of modern quality control.3 During his lectures in Japan in the early 1950s, Deming noted that the Japanese participants shortened the cycle’s steps to the now traditional plan, do, check and act. Plan, Do, Check, Act (PDCA) is a continual improvement methodology championed by one of the founding fathers of quality management, Dr. A Plan-Do-Check-Act model (PDCA) or Plan-Do-Study-Act (PDSA) model can be applied to improve an overall business as well as individual projects.
In my last posts I explained the PDCA (Plan, Do, Check, Act), common mistakes, and its history.However, there is a whole fruit stand of additional versions with some modifications that have popped up:. PDCA is an improvement cycle based on the scientific method of proposing a change in a process, implementing the change, measuring the results, and taking appropriate action. The Plan-Do-Check-Act (PDCA) cycle, also known as the Deming wheel or the Deming cycle, is an iterative method for continual improvement of processes, products, or services and is a key element of lean management.
¾ Avoid the common disconnects as seen by one professional in industry, such as over/under-planning and not validating the. When using the PDSA cycle, it's important to include internal and external customers;. Just as a circle has no end, the PDCA cycle should be repeated again and again for continuous improvement.
PDSA, or Plan-Do-Study-Act, is an iterative, four-stage problem-solving model used for improving a process or carrying out change. Edwards Deming.PDCA is an approach that emphasizes, once improvements have been identified and implemented, we should then seek out. Well PDCA (which stands for Plan-Do-Check-Act) is an offshoot of Lean.
The Plan-Do-Study-Act (PDSA) method is a way to test a change that is implemented. In fact, the name PDCA was coined by participants of his lectures, who streamlined the Shewhart Cycle to “Plan, Do, Check, Act.” Deming actually preferred “Study” to “Check,” making it the Plan-Do-Study-Act or PDSA cycle, as the word placed more emphasis on analyzing results rather than simply checking what had changed. Both being a scientific, process oriented, approach to solving problems efficiently and effectively.
In the PDCA cycle, the work process is cyclical and supported by four pillars (Planning / Development / Check / Action). It is during the ‘Check’ phase that the actual measurement and analysis of deviation from plan versus the records are evident during execution. The PDCA cycle consists of four steps:.
Application of PLAN DO CHECK ACT ABC Co. We believe, however, that the model is deficient, and that it is easy to improve it. Key performance indicators link these steps together, creating a process of continuous improvement.
And these actually constitute the Acronym of the PDCA cycle:. PDCA is an acronym for a change management, and continuous improvement process. PDCA ("Plan-Do-Check-Act") is an iterative four step problem solving process typically used in quality control.
PDCA มีหลากหลายหลักการที่ทำให้เราไปถึงความสำเร็จที่เราตั้งใจไว้ ซึ่งถ้าลองวิเคราะห์โดยใช้หลักการ Plan – Do – Check – Act เป็นกรอบในการ. William Edwards Deming in the 1950s (which is why it’s sometimes called the ‘Deming Wheel.’). It involves systematically testing possible solutions, assessing the results, and implementing the ones that have shown to work.
Use the PDCA cycle when:. The Plan-Do-Check-Act (PDCA) Cycle is a four-step problem-solving iterative technique used to improve business processes. PDCA emerged from a lecture given by Deming in Japan in 1950.
The approach is iterative - that is, it is a cycle. But in fact, the PDCA concept (or cycle) emerged in the 1930s, designed by American Walter Andrew Shewhart. It is also known as the Deming circle / cycle / wheel, the Shewhart cycle, the control circle / cycle, or plan–do–study–act (PDSA).
Here we take action on what is not working as planned. Starting a new improvement project. Quality Improvement Process Using Plan, Do, Study, Act (PDSA) – Planning for Action Kathy Hybarger, RN, MSN Connie Steigmeyer, RN, MSN Betsy Lee, RN, MSPH.
PDCA activities consist of four steps namely Plan, Do, Check, and Action with repeated stages forming like a circle. The basis of the PDCA cycle is a four-part quality lifecycle. The Plan-do-check-act cycle (Figure 1) is a four-step model for carrying out change.
PDCA's acronym's cause confusion--both "Do" and "Act" mean the same;. Plan-do-check-act, or PDCA, is a method organizations use to continually improve their internal processes, increasing the quality of their products and the overall efficiency of their business. If the changes are not as planned then continue the cycle to achieve the goal with a different plan.
PDCA。そう、PDCAです。ビジネスマンであれば知らない人はいないんじゃないかと思うぐらい有名な改善サイクルの1つですね。 ところで、そのPDCAってなんの略なんでしょうか? 一番一般的なのは、 P:. Central to the scientific method, problem solving and continuous improvement, the PDCA cycle stands for Plan, Do, Check, and A is for Act, Adjust or Action. This inherent fault relates to the shortcomings from adaptation of the original Japanese methodology.
PDSA, SDCA, OODA, ODCA, DMAIC, LAMDA, FACTUAL, Kata, and 8D – and probably more that I do not know of.

Plan Do Check Act Early Childhood Training And Technical Assistance System
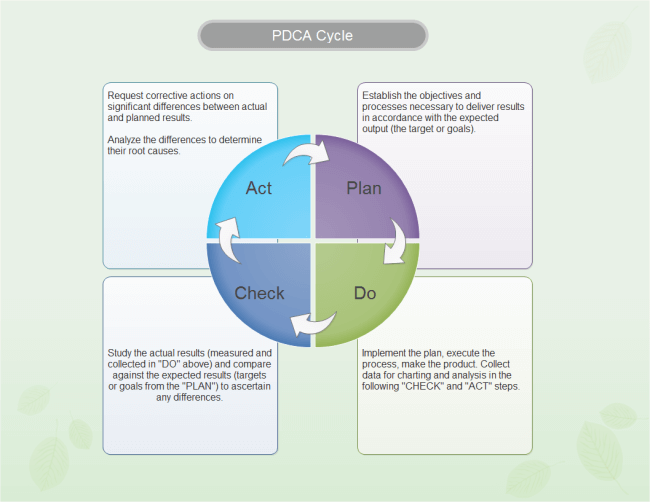
Plan Do Check Act Pdca A Comprehensive Guide Edrawmax
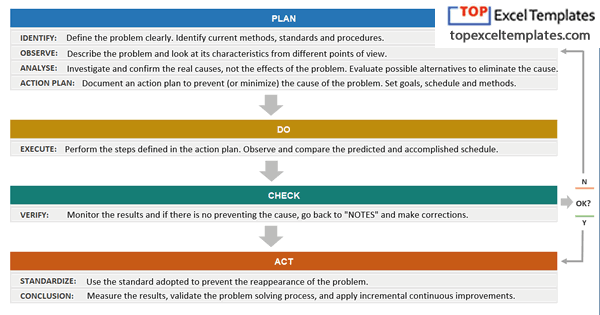
Simple Pdca Excel Template Free Deming Cycle Spreadsheet Example

The Four Steps Of Pdca And How They Lead To Continuous Improvement

The Plan Do Check Act Cycle Free Management Books
Using The Pdca Cycle To Support Continuous Improvement Kaizen

Pdca Plan Do Check Act Deming Cycle Diagram Method Infographic Royalty Free Cliparts Vectors And Stock Illustration Image

What Is Plan Do Check Act Pdca Cycle Kanbanize
Q Tbn 3aand9gcqw M2rspqmmc2miofhqd7sdp9zzq3cztxfztiorrrmxyz 5rjx Usqp Cau
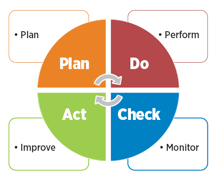
Pdca Cycle What Is The Plan Do Check Act Cycle Asq
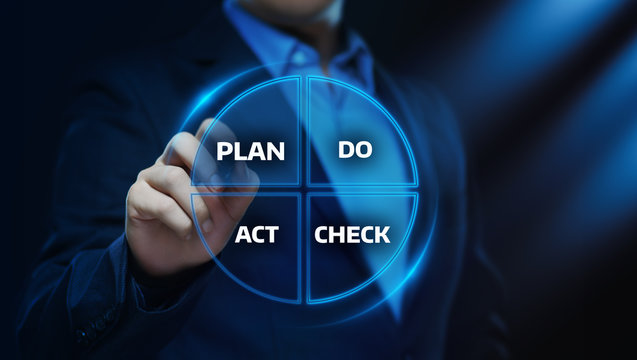
Pdca Photos Royalty Free Images Graphics Vectors Videos Adobe Stock

Plan Do Check Act 24 7 We Never Stop Thinking Pdca 24 7 We Start With A Results Focused Purpose Driven Massive Action Plan And Push It Through The Cont
85 Plan Do Check Act Pdca Stock Photos Pictures Royalty Free Images Istock

Pdca Wikipedia
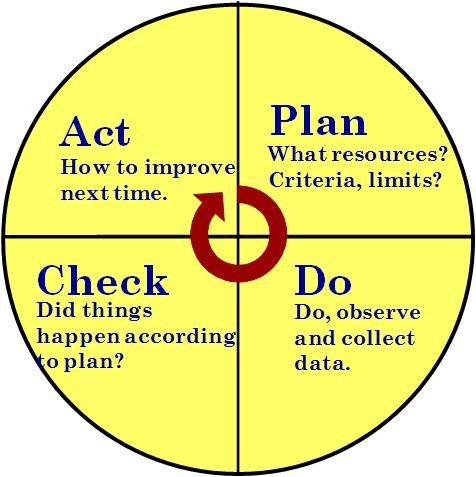
How To Master Iso 9001 Pdca Cycle Plan Do Check Act
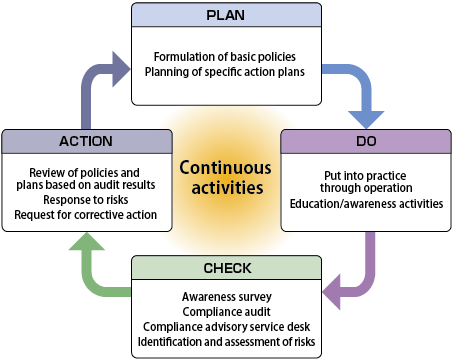
Pdca Plan Do Check Act Human Performance Technology Manual
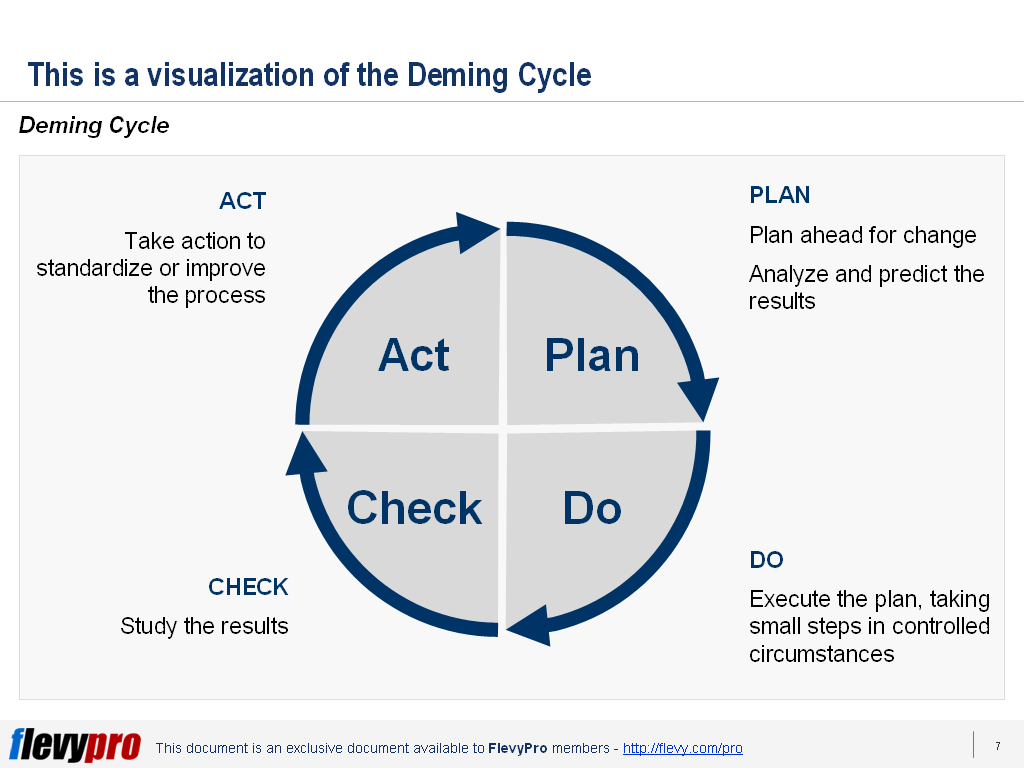
Continuous Improvement 101 The Deming Cycle Pdca Flevy Com Blog
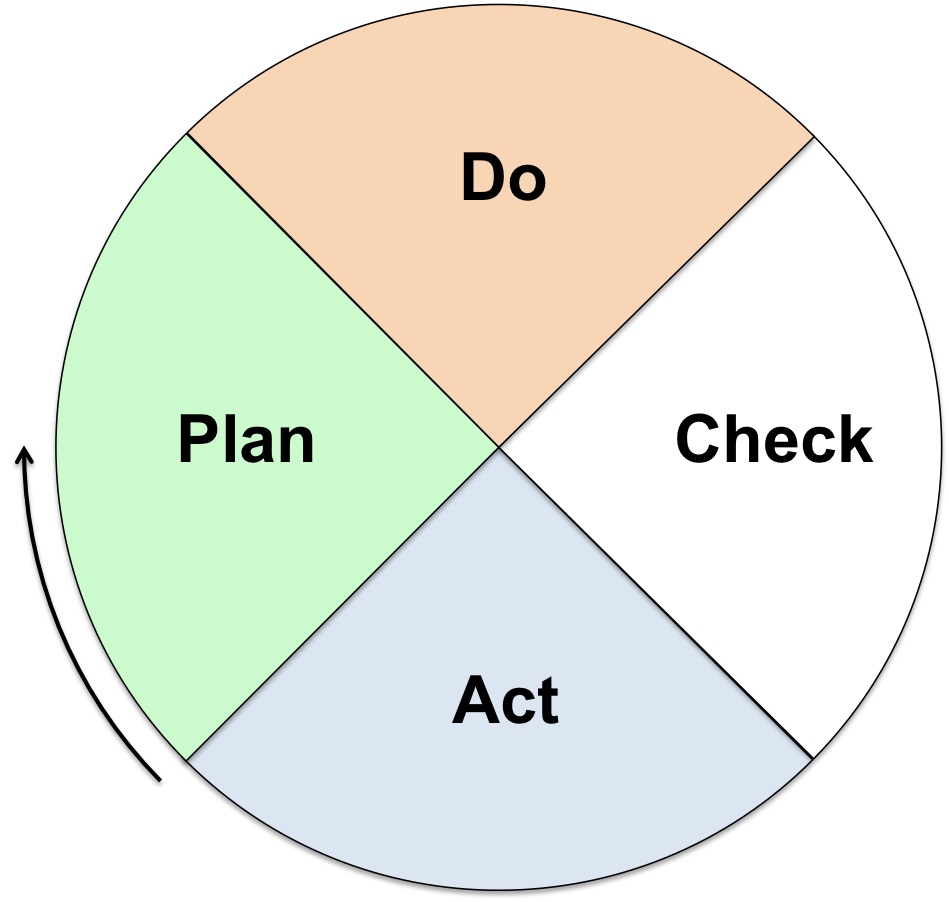
Pdca Plan Do Reflect Improve Um Sorry I Mean Check Act It S A Delivery Thing
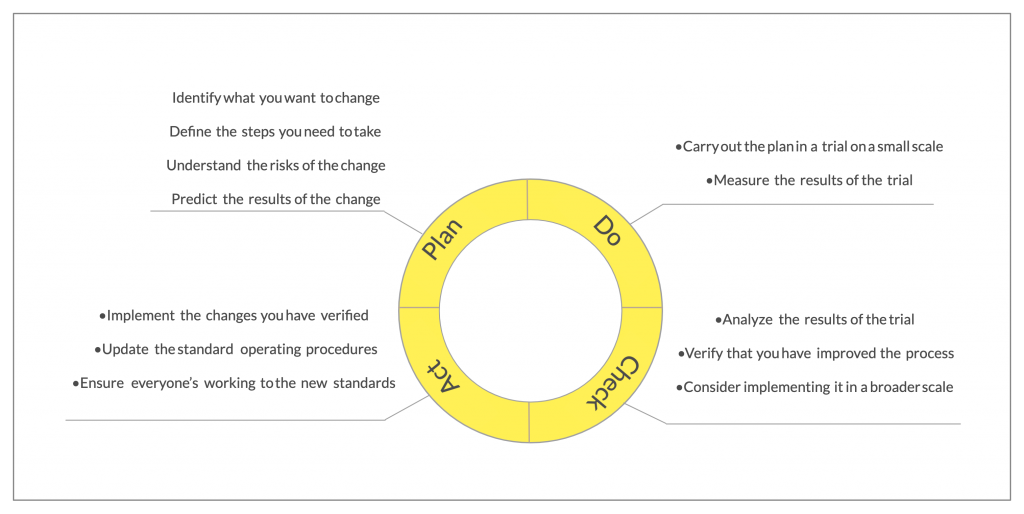
Pdca Cycle A Comprehensive Guide To Plan Do Check Act

Understanding The Pdca Cycle Centuryqsm

What Is Plan Do Check Act Pdca Cycle Kanbanize

Pdca The 4 Steps Of Effective Marketing By Analytics That Profit Medium
Q Tbn 3aand9gcr3mdu80vo4aqashuc9fdqf7vuqeiu41onm Jwnjpy2fwuqrbcx Usqp Cau
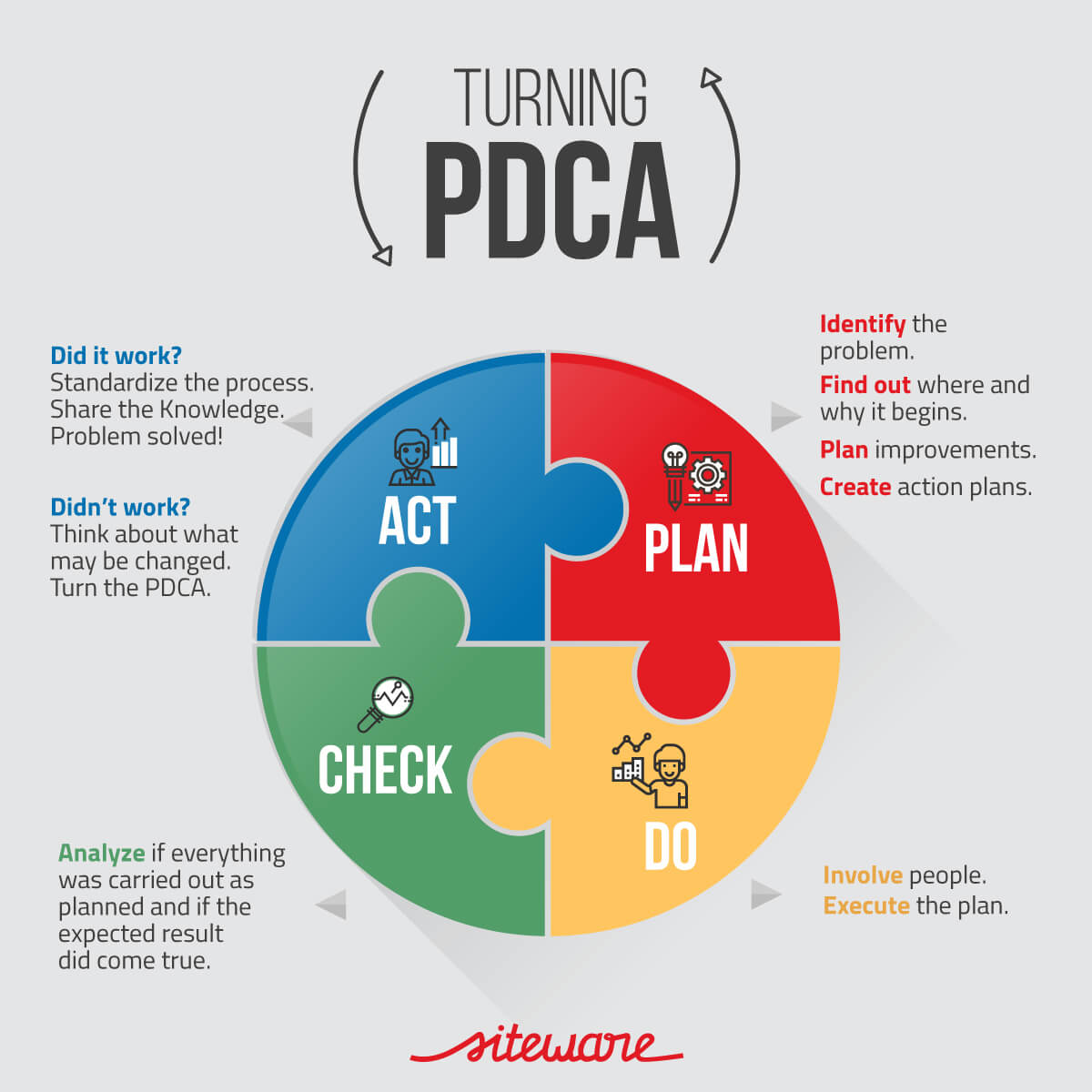
How To Do Pdca Step By Step Everything You Need To Know

16 The Principles Of Pdca Management Plan Do Check Act Usually Is Download Scientific Diagram
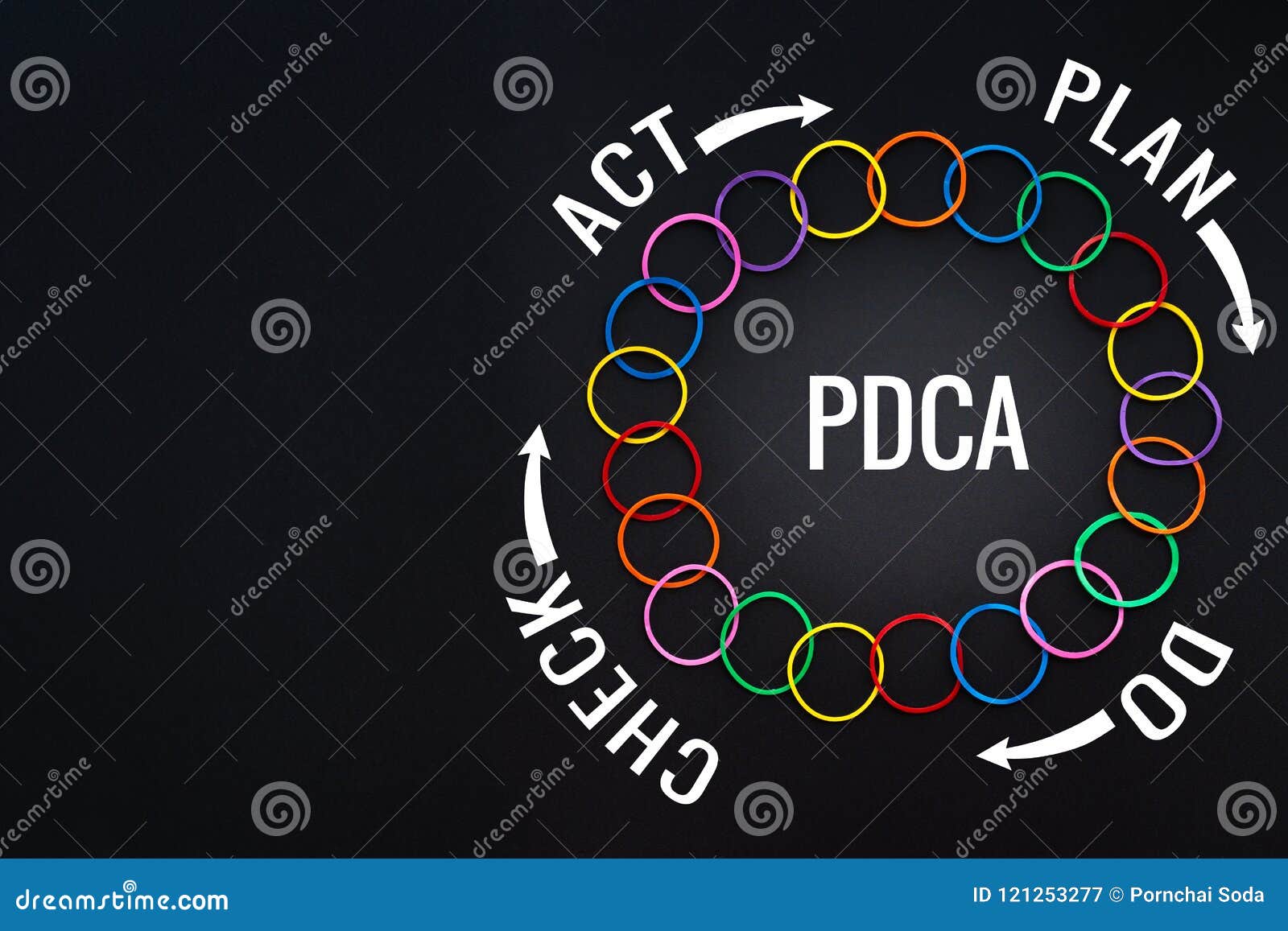
Pdca Process Improvement Action Plan Strategy Colorful Rubber Band On The Black Backgrounds With Text Plan Do Check And Act Stock Image Image Of Band Backgrounds

The Effectiveness Of The Plan Do Check Act Pdca Cycle

Kaizen Via Plan Do Check Act Pdca Lean Six Sigma Belgium

Pdca Plan Do Check Act Extended Diagram Karn Bulsuk Full Speed Ahead
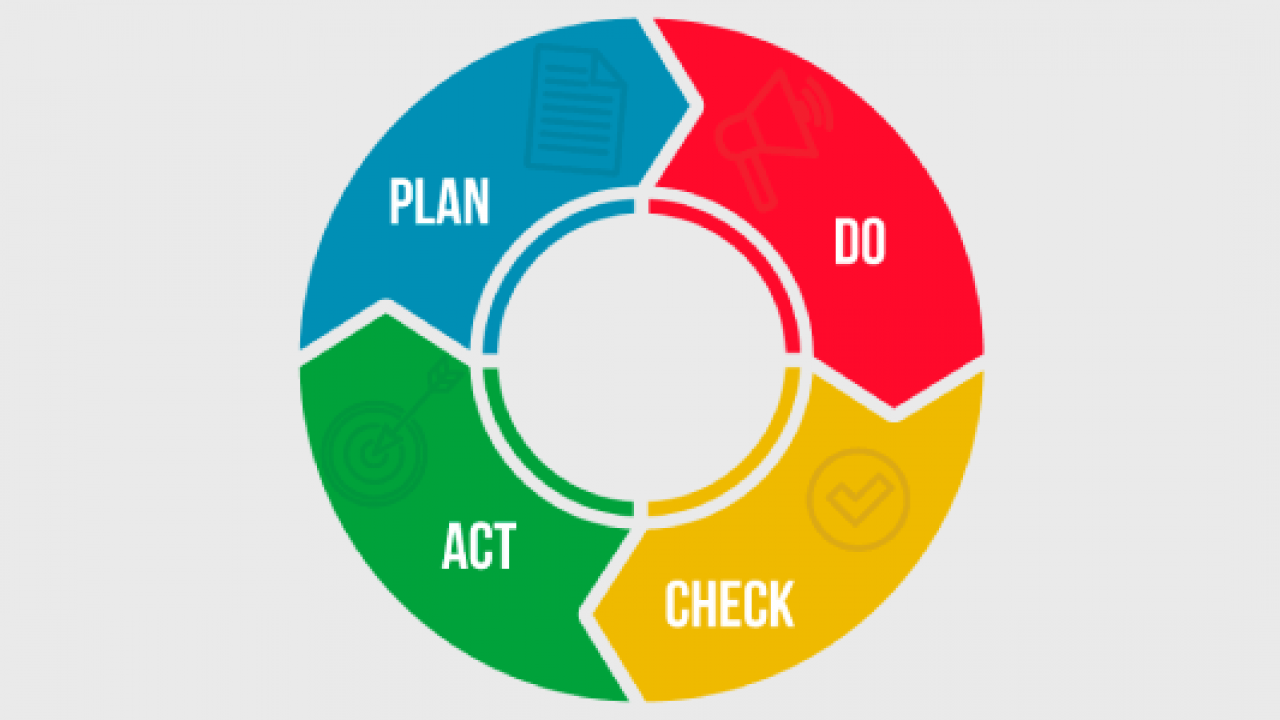
How To Do Pdca Step By Step Everything You Need To Know

Pdca Plan Do Check And Act
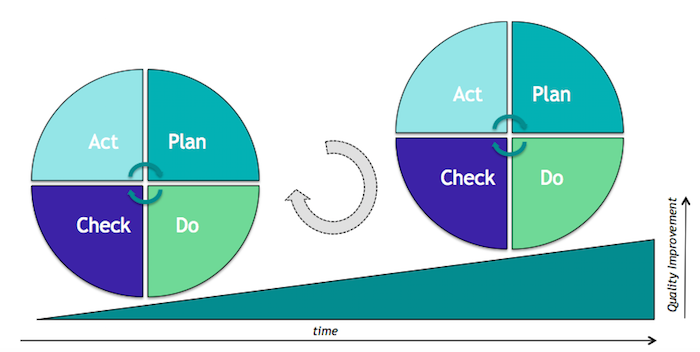
Ict Institute Information Security And Pdca Plan Do Check Act

Pdca Cycle Example Business Process Management How To Plan Online School College
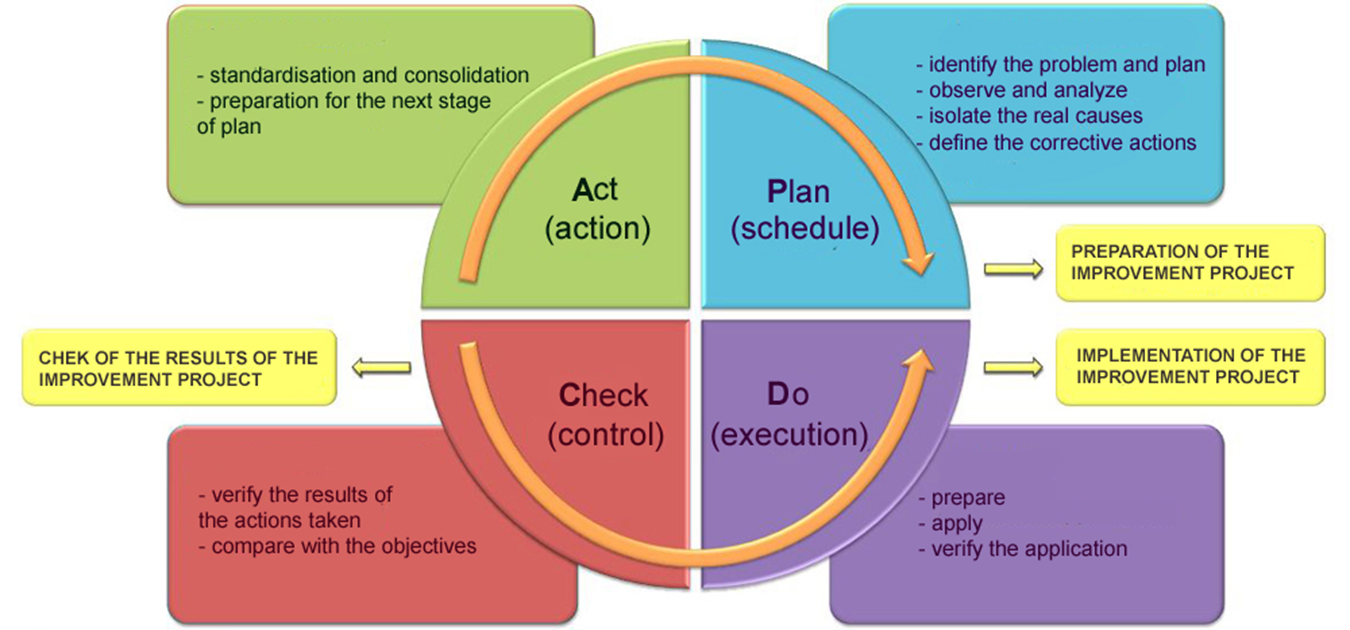
Pdca Plan Do Check Act The Blog Of Logistics At Mgeps At Upv

What Is Plan Do Check Act Pdca Cycle Kanbanize
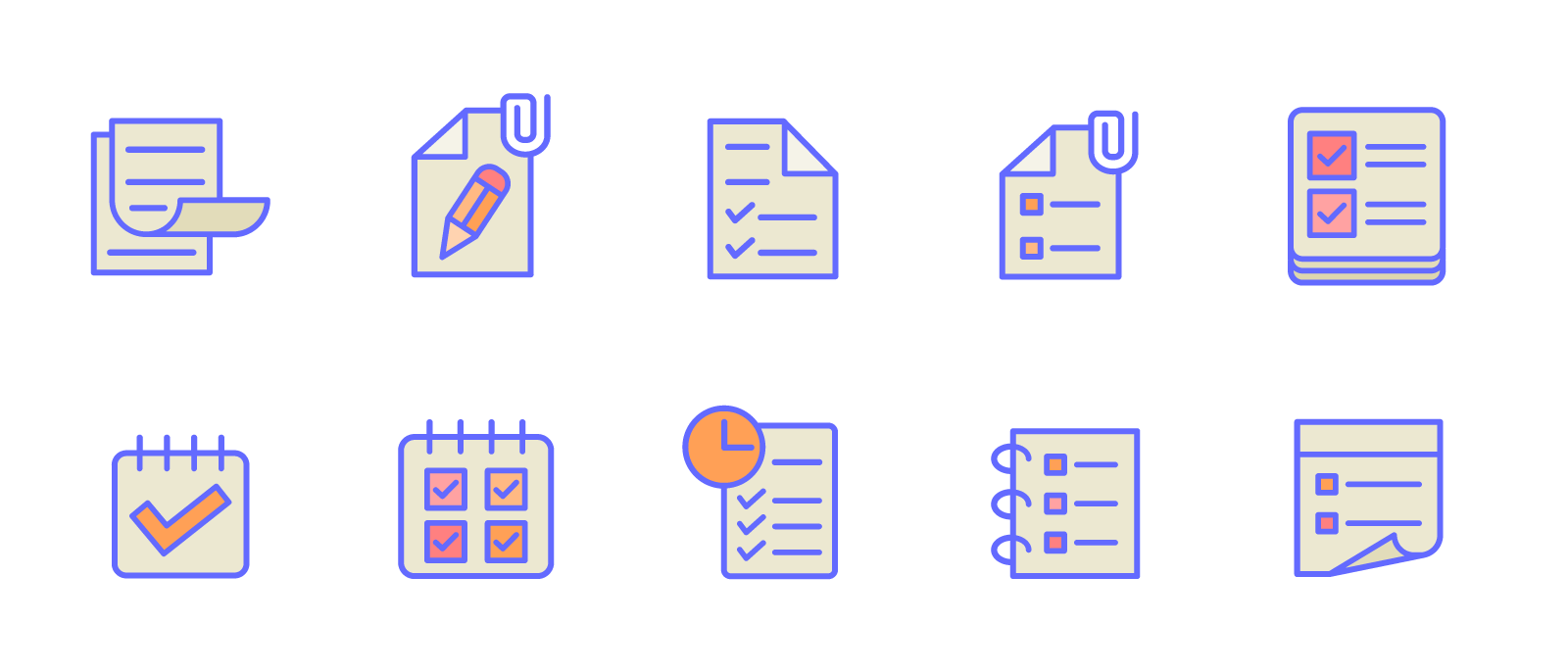
How To Apply The Plan Do Check Act Pdca Model Lucidchart Blog

Pdca Cycle In Cycle How To Plan Business Powerpoint Templates

The Pdca Cycle In Energy And Utilities Management Viridis
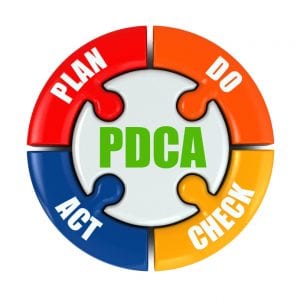
Using Job Tasks For More Efficient Pdca Cycles
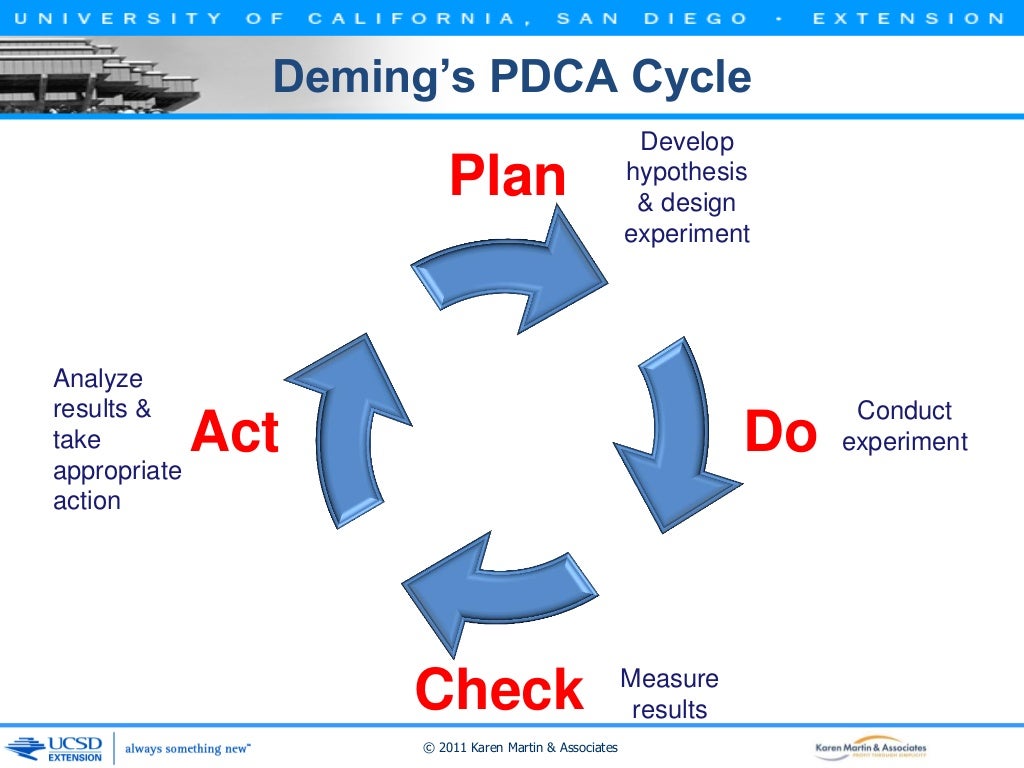
Deming S Pdca Cycle Plan Analyze

Amazon Com Pdca Plan Do Check Act Poster 22 X 28 Made In The Usa Office Products
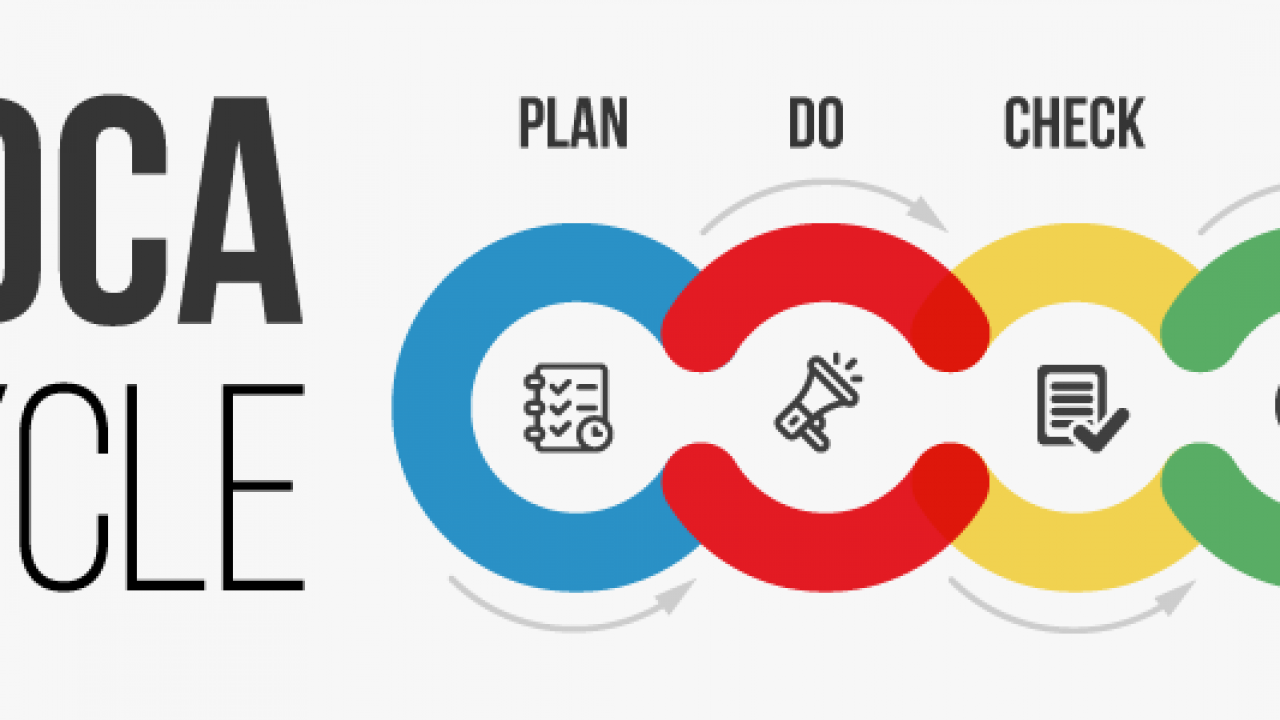
What Is The Pdca Cycle How Does It Improve Your Management

What Is Plan Do Check Act Pdca Cycle Kanbanize

Using Plan Do Check Act Pdca To Process Teambuilding Activities How To Plan Process Control Team Building Activities
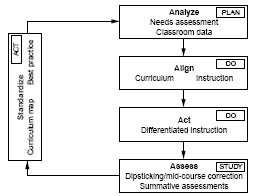
Pdca Cycle What Is The Plan Do Check Act Cycle Asq
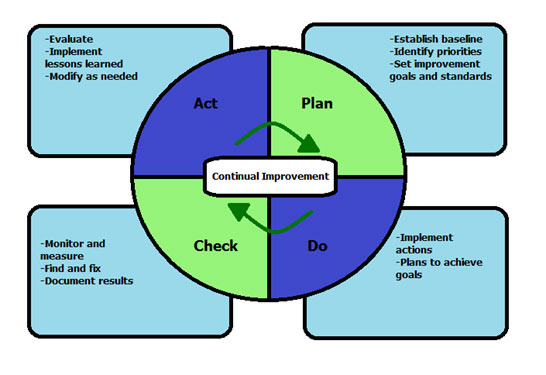
Nems Plan Do Check Act

The Effectiveness Of The Plan Do Check Act Cycle Business Enterprise Mapping
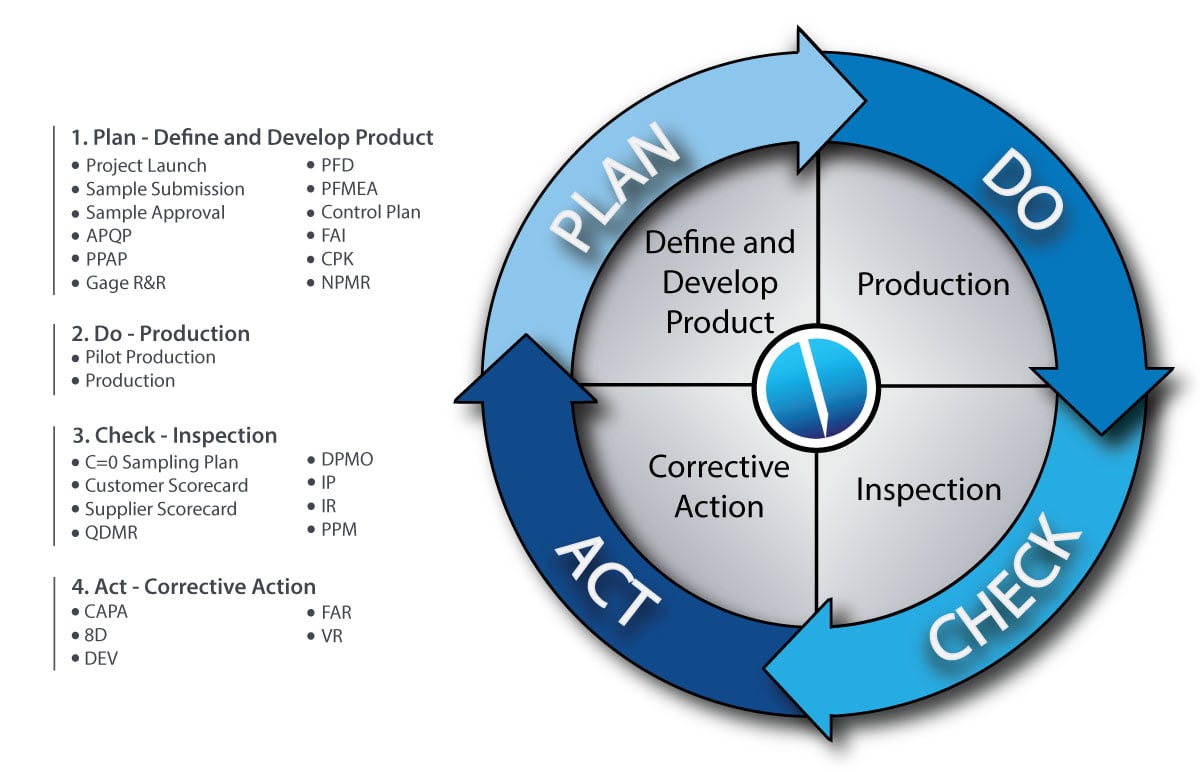
How To Implement The Pdca Cycle Plan Do Check Act Free Template

Pdca How To Eliminate Error In Your Processes And Products Process Street Checklist Workflow And Sop Software
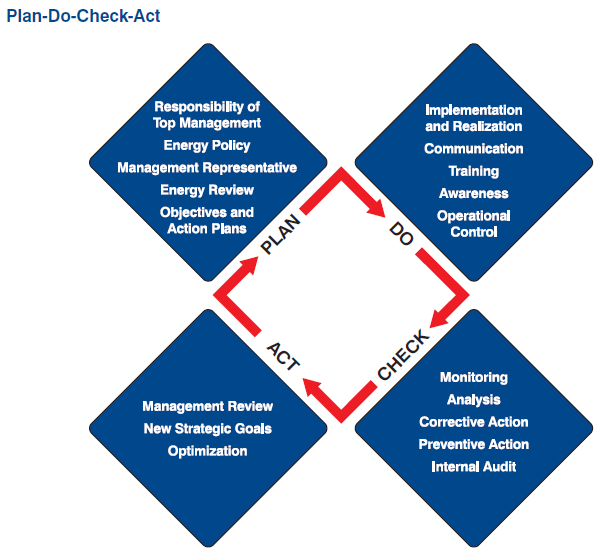
Energy Management Plan Do Check Act

How To Use The Plan Do Check Act Pdca Method Successfully In The Home
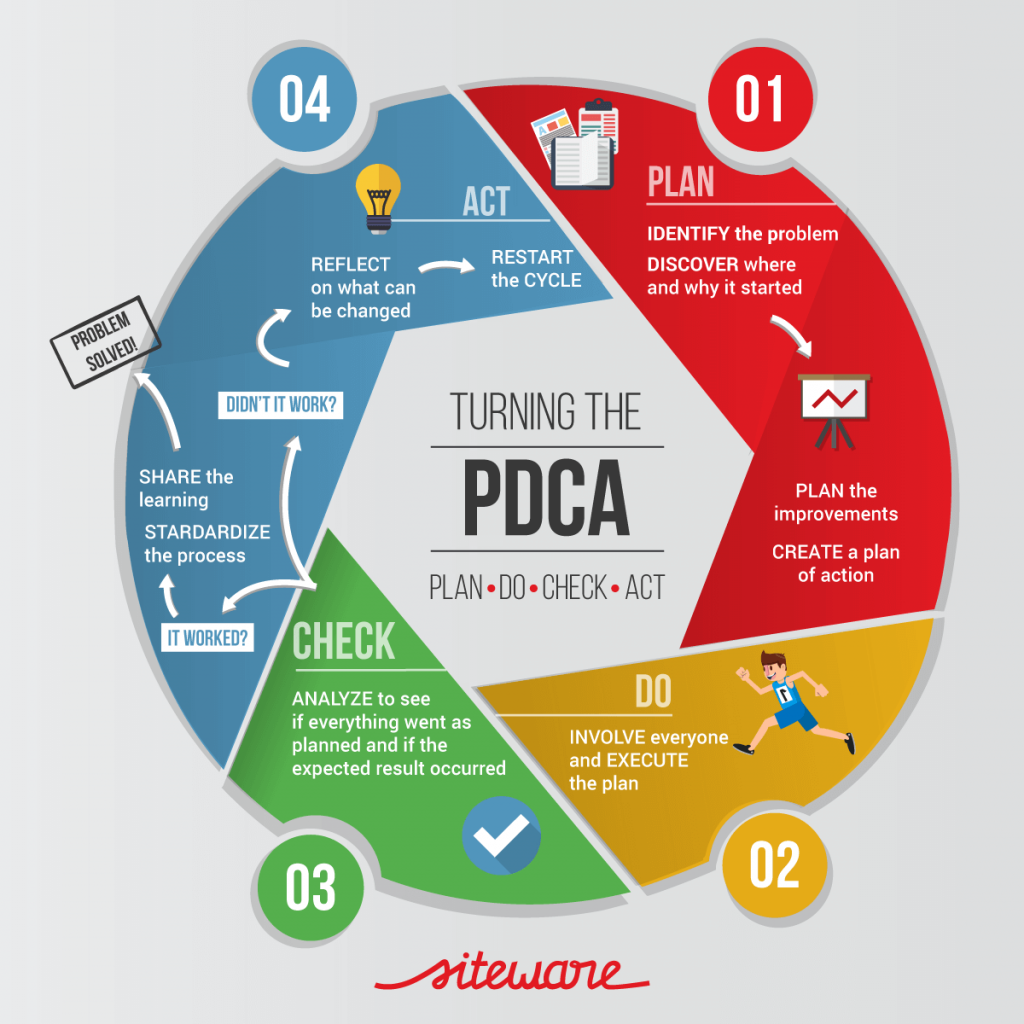
What Is The Pdca Cycle How Does It Improve Your Management

The Plan Do Check Act Pdca Cycle Ppt Slide Powerpoint Presentation Slides Ppt Slides Graphics Sample Ppt Files Template Slide

Pdca Plan Do Check Act Template
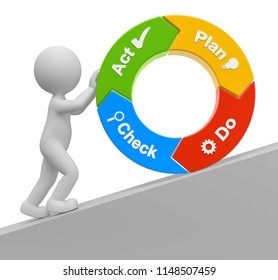
Pdca Cycle Images Stock Photos Vectors Shutterstock

Free Art Print Of Pdca Plan Do Check Act Business Woman Do Pdca Plan Do Check Action For Business Continuous Improvement Freeart Fa
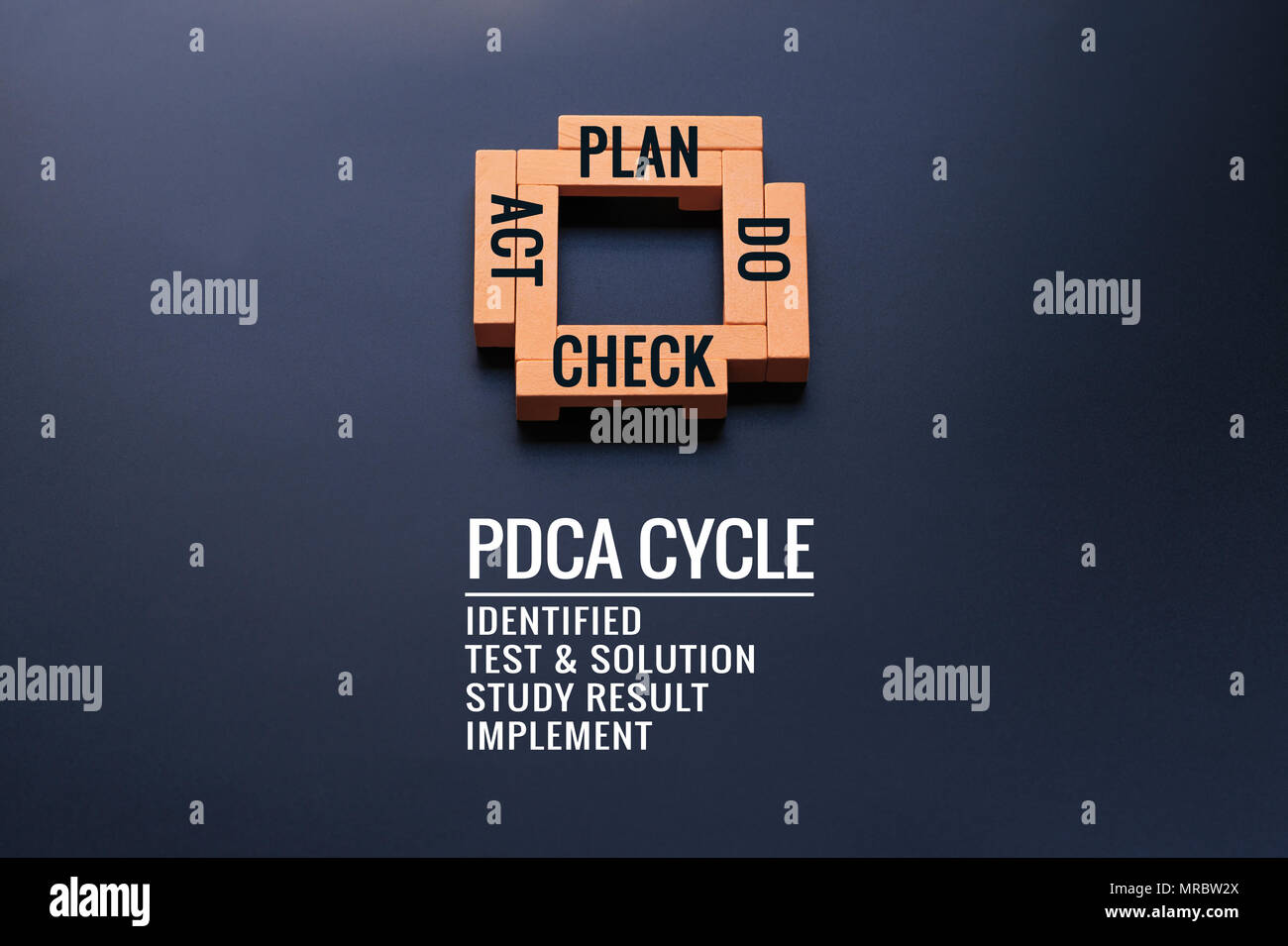
Pdca Cycle Process Improvement Action Plan Strategy Wooden Square On The Black Backgrounds With Text Plan Do Check And Act With Copy Space Stock Photo Alamy
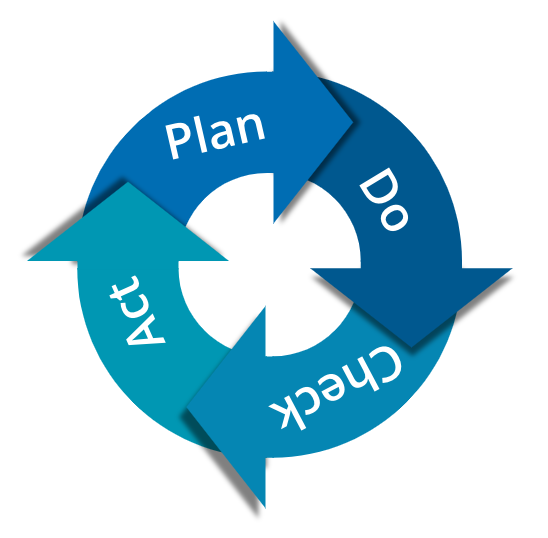
Action Plan How To Be More Effective When Managing It

How Do I Use Plan Do Check Act To Manage Safety Well

Pdca Form
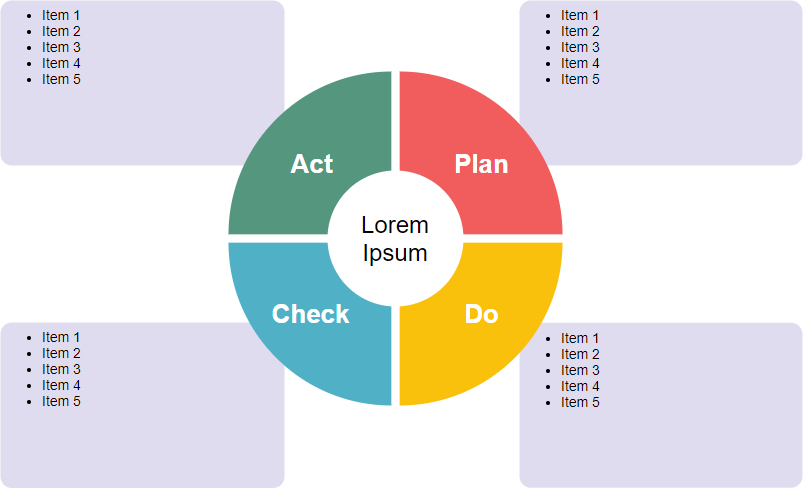
Agile Lean Approach With Plan Do Check Act Cycle

Plan Do Check Act In The Lean Lexicon C

How Pdca Relates To Business Continuity Avalution
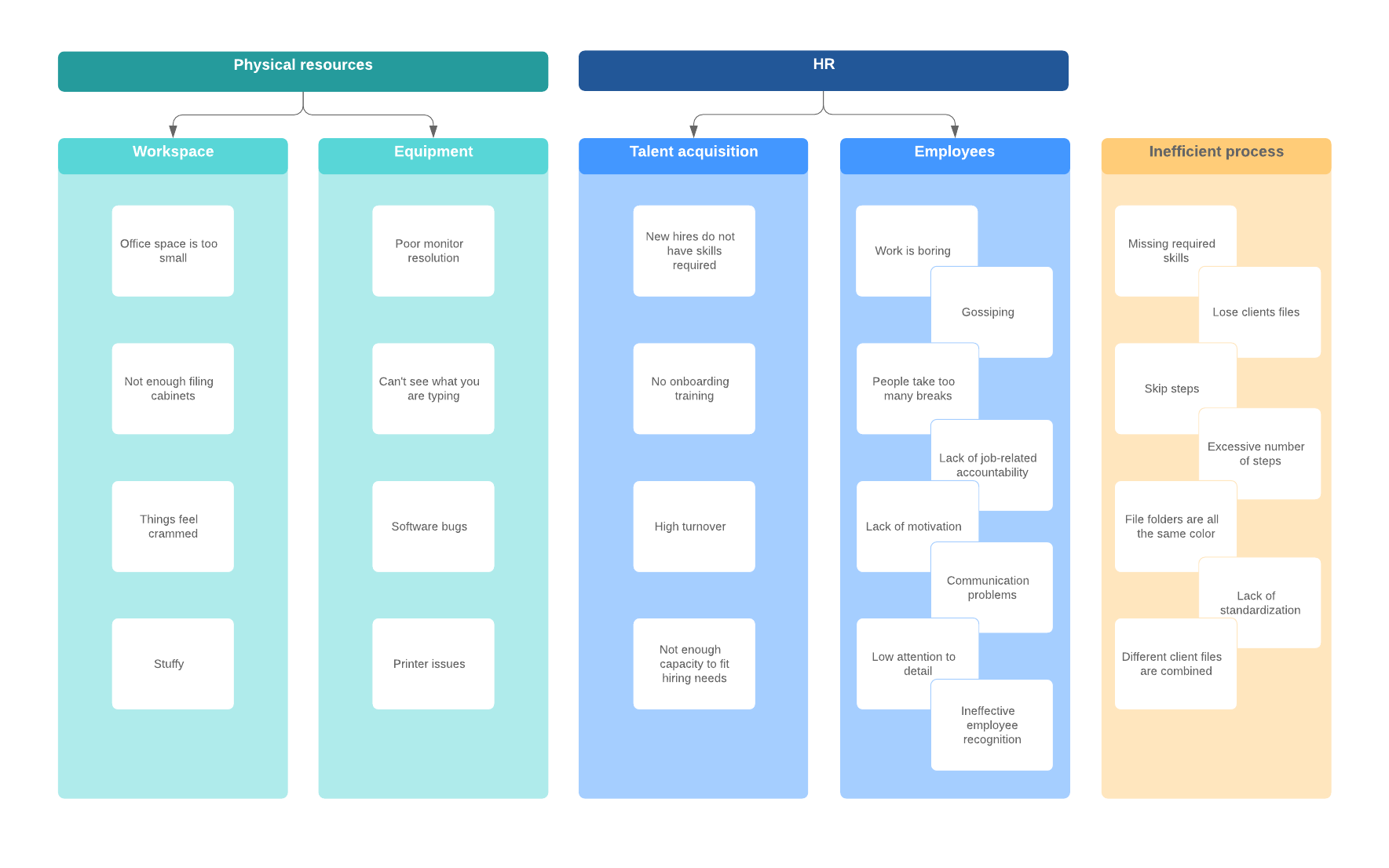
How To Apply The Plan Do Check Act Pdca Model Lucidchart Blog

How To Use The Pdca Cycle To Improve Your Business

Pdca Wikipedia
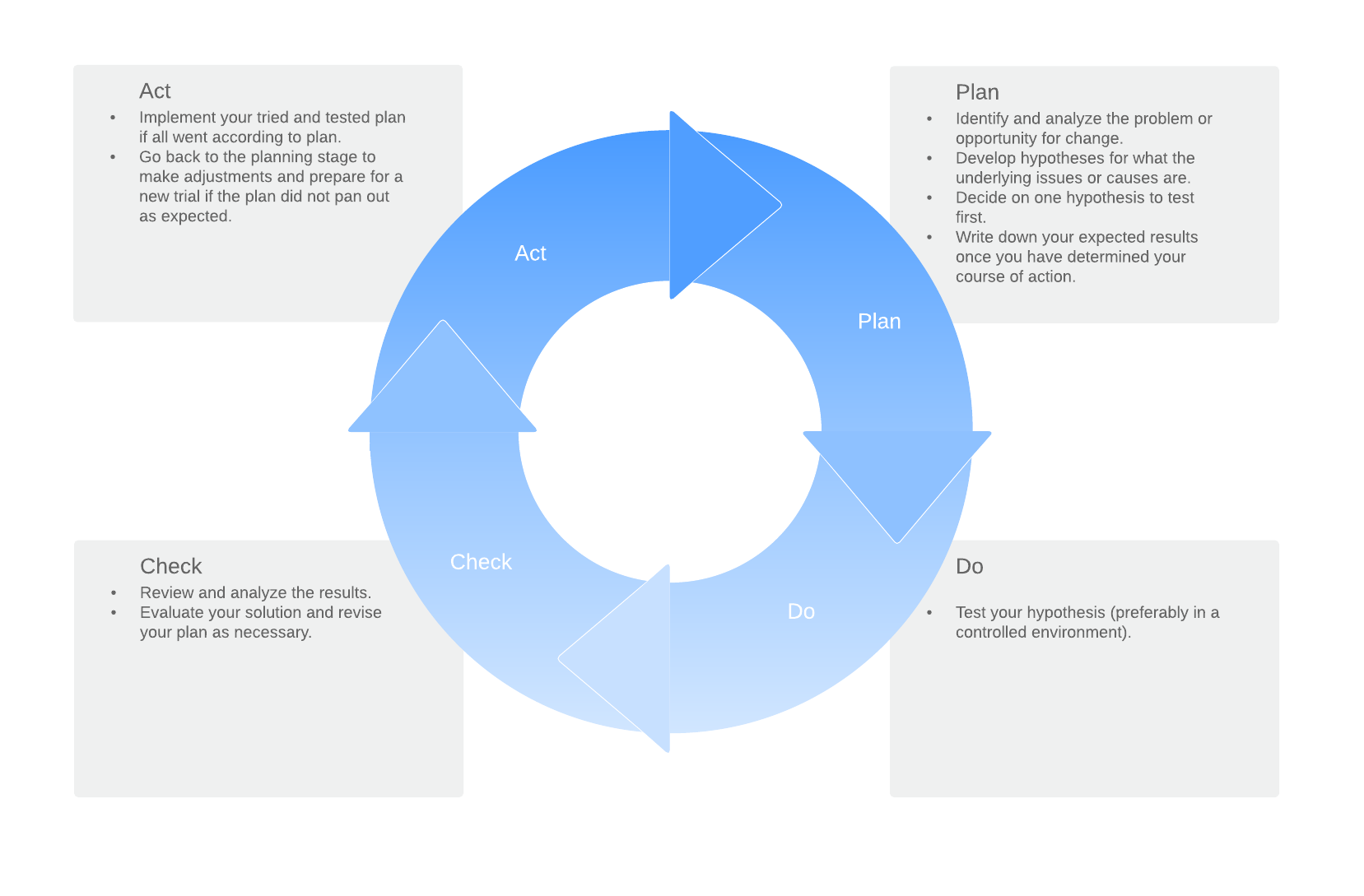
How To Apply The Plan Do Check Act Pdca Model Lucidchart Blog
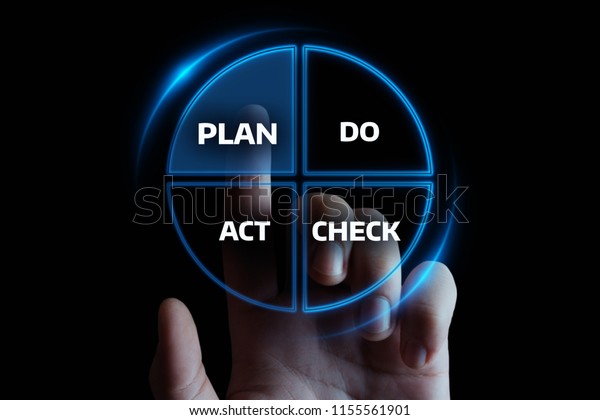
Pdca Plan Do Check Act Business Stock Photo Edit Now
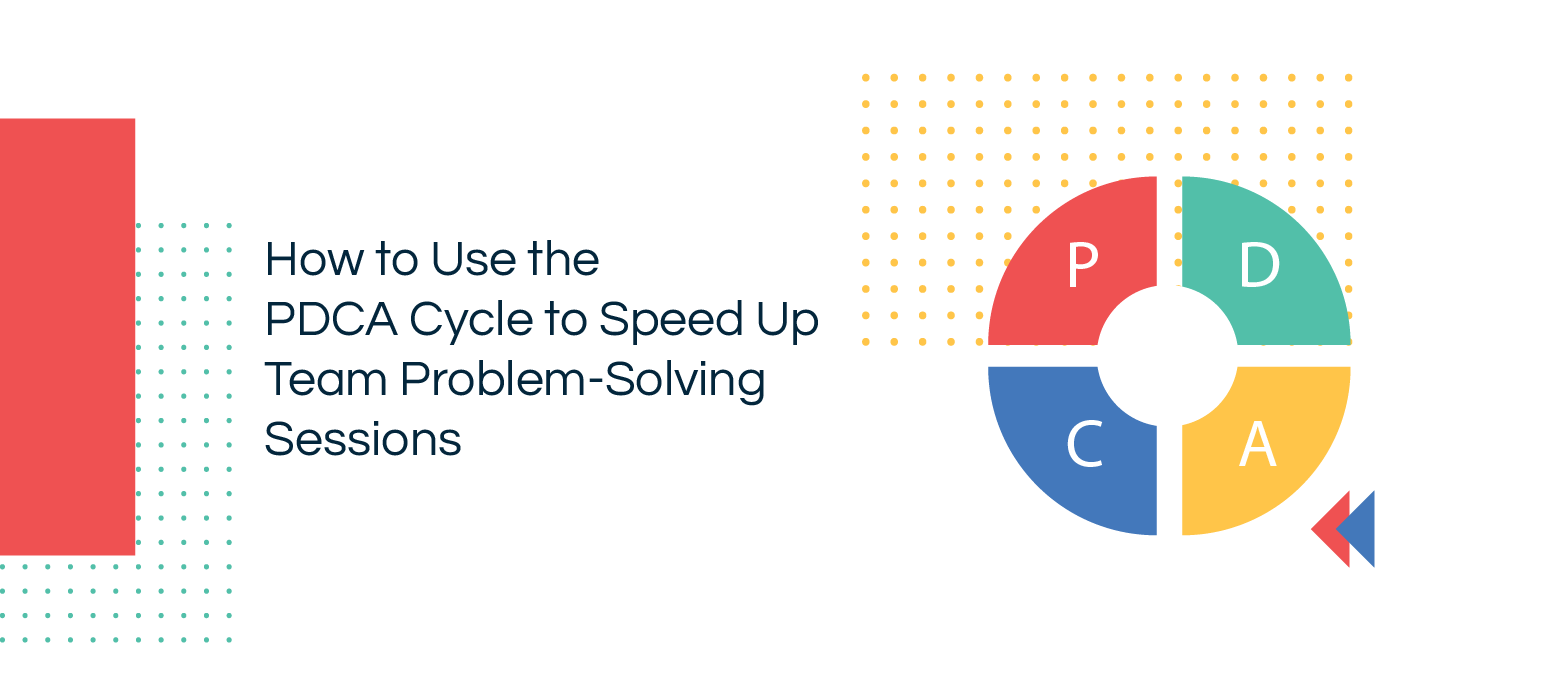
Pdca Cycle A Comprehensive Guide To Plan Do Check Act

Flat 3d Isometric Businessman Standing In Front Of Pdca Plan Royalty Free Cliparts Vectors And Stock Illustration Image

Plan Do Check Act Pdca Implementing New Ideas In A Controlled Way Colleaga

The Pdca Cycle In Energy And Utilities Management Viridis

Managing Inspections In Accordance With The Pdca Plan Do Check Act Method
Q Tbn 3aand9gcqo38jcpdebvlxbrx9ir6jd0x6plhapz4dhmxnyaevvanxlccbg Usqp Cau
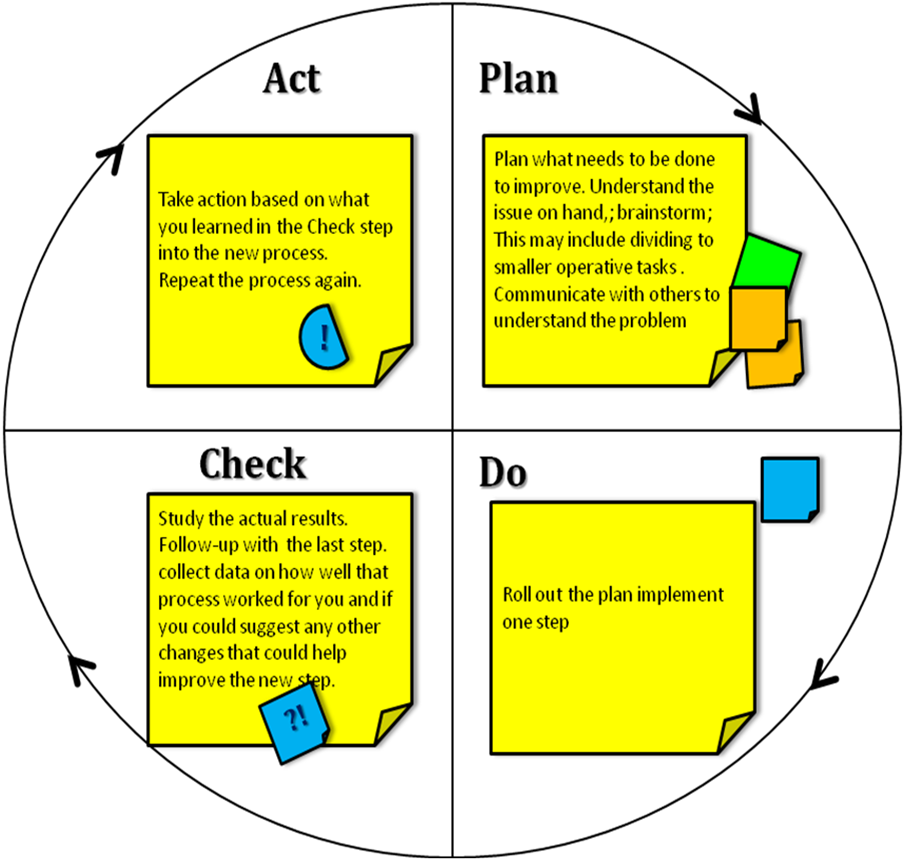
Your Family Agile And You Pdca Psychology Continues Improvement And Kids Video Games
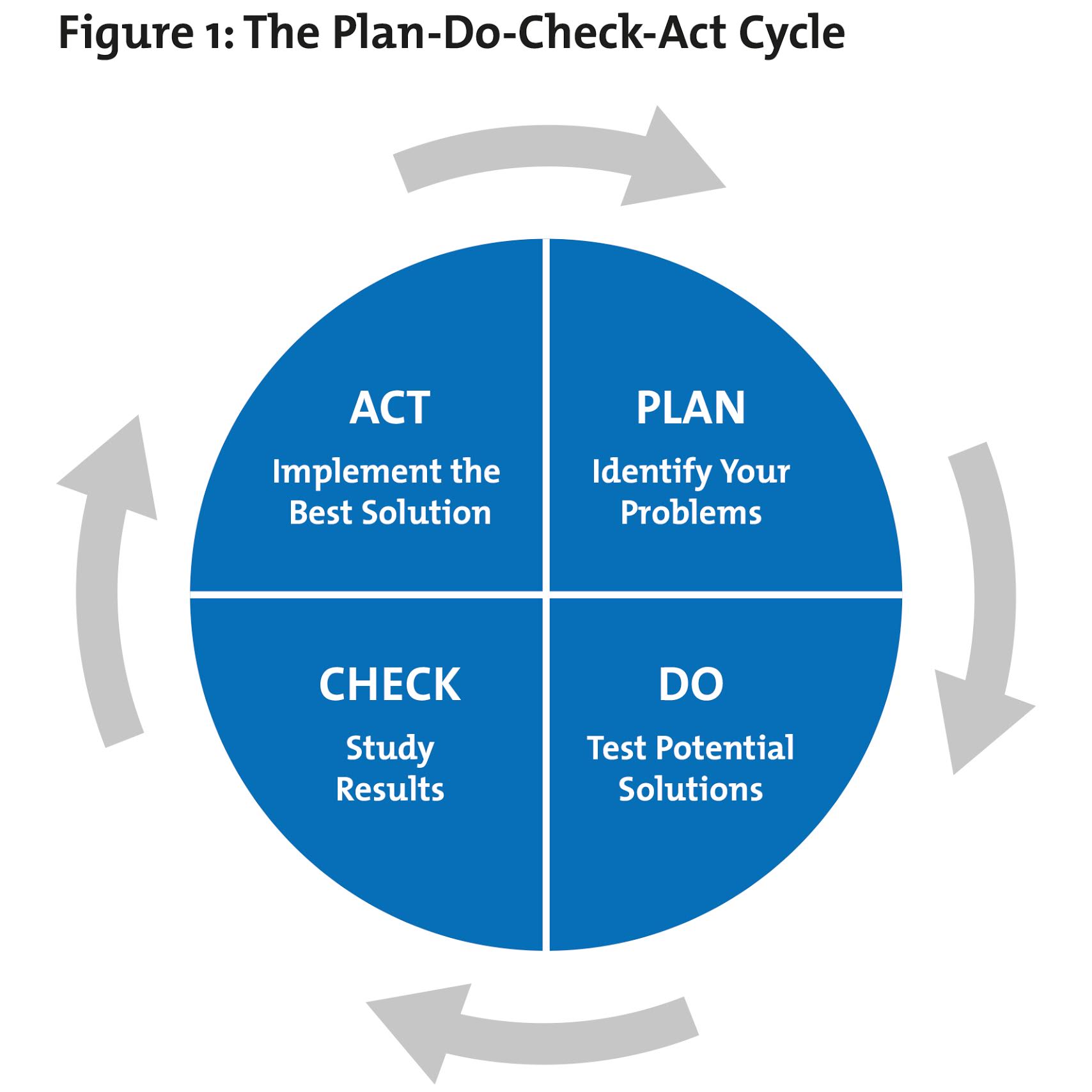
Plan Do Check Act Pdca From Mindtools Com
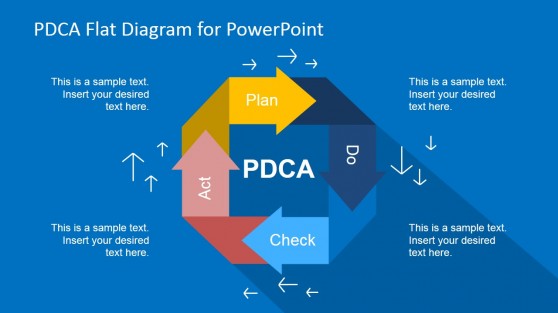
Plan Do Check Act Powerpoint Templates Pdca
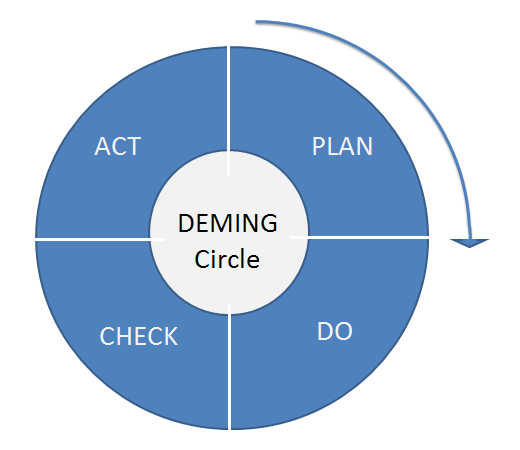
How To Use Pdca Cycle To Improve Process Efficiency Tallyfy

The Key To Lean Plan Do Check Act Allaboutlean Com
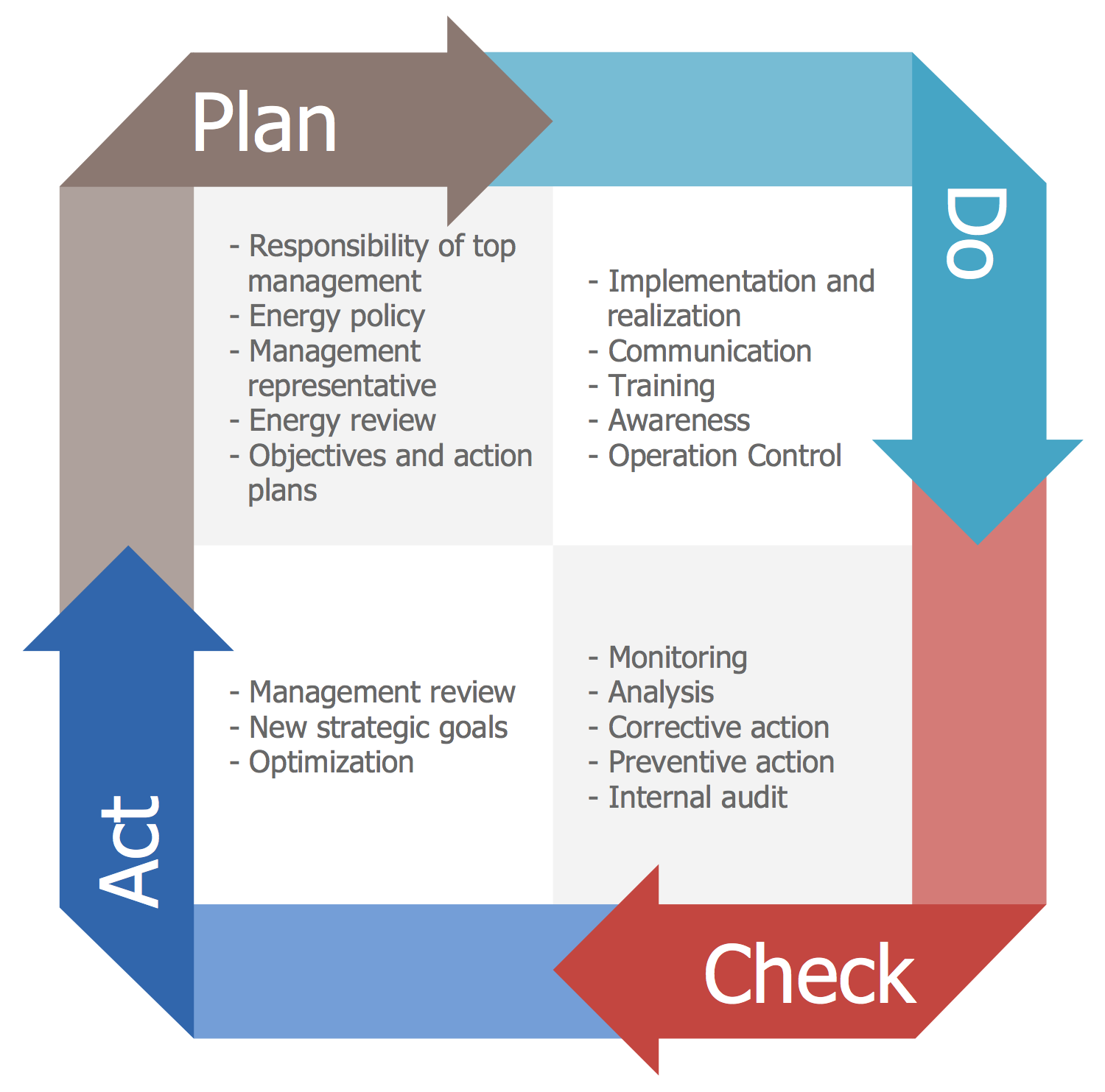
Plan Do Check Act Pdca Solution Conceptdraw Com

Plan Do Check Act Pdca Model See Online Version For Colours Download Scientific Diagram

My Pdca A Perfect Companion For All Professionals Bexsolutionz

Pdca In Interface Lean Analytics Association

The Humble Extraordinary Pdca The Kaizen Way

Apply The Pdca Cycle For Continuous Improvement On Epci Project Mande Blog

Ict Institute Information Security And Pdca Plan Do Check Act
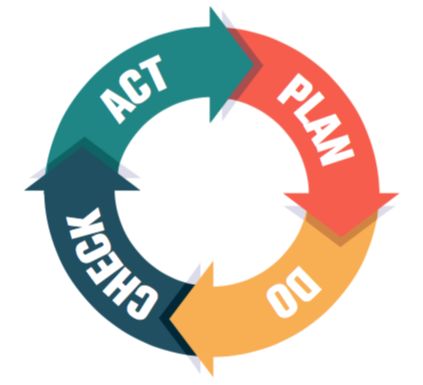
Pdca Cycle Plan Do Check Act Creative Safety Supply
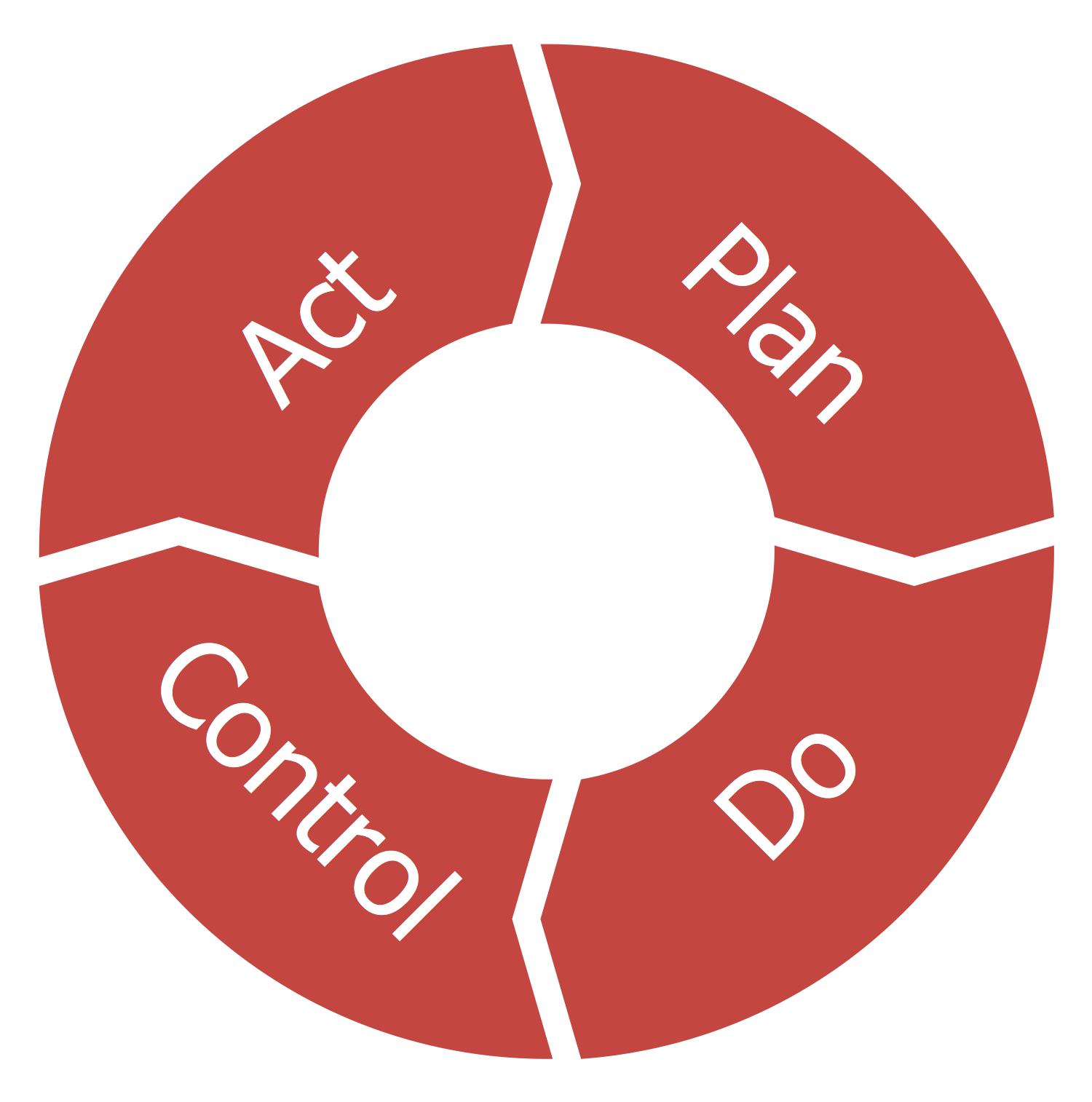
Plan Do Check Act Pdca Solution Conceptdraw Com
1
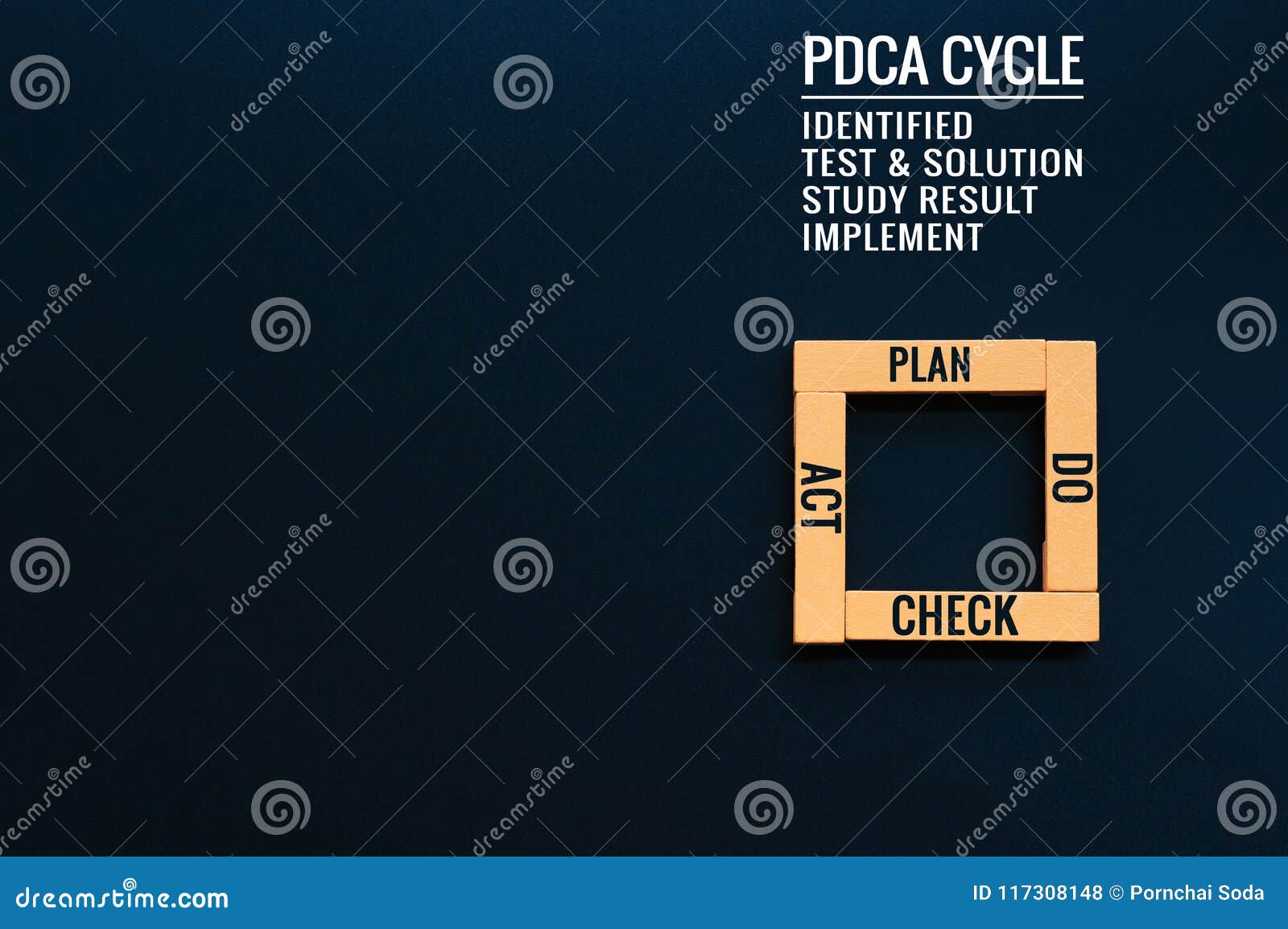
Pdca Cycle Process Improvement Action Plan Strategy Wooden Square On The Black Backgrounds With Text Plan Do Check And Act Stock Photo Image Of Continuous Change

Plan Do Check Act Cycle Source Management Systems Consulting
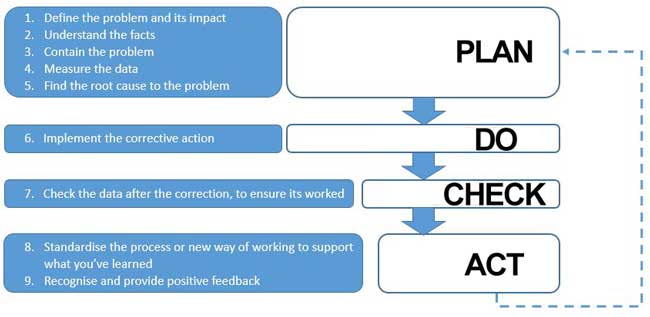
Plan Do Check Act A Simple 4 Step Problem Solving Methodology Educational Business Articles

Implementing 5s With P D C A Cycle Download Scientific Diagram
.jpg?width=516&name=PDCA%20(2).jpg)
Plan Do Check Act

What Is Plan Do Check Act How Do You Use Pdca

What Is Plan Do Check Act Pdca Cycle Kanbanize

The Iso 9001 15 Standard And The Plan Do Check Act Cycle Qualitywbt

Continuous Improvement With Pdca As A Qa An Important Part Of Your Tasks By Mohammed Amine Rouh Medium